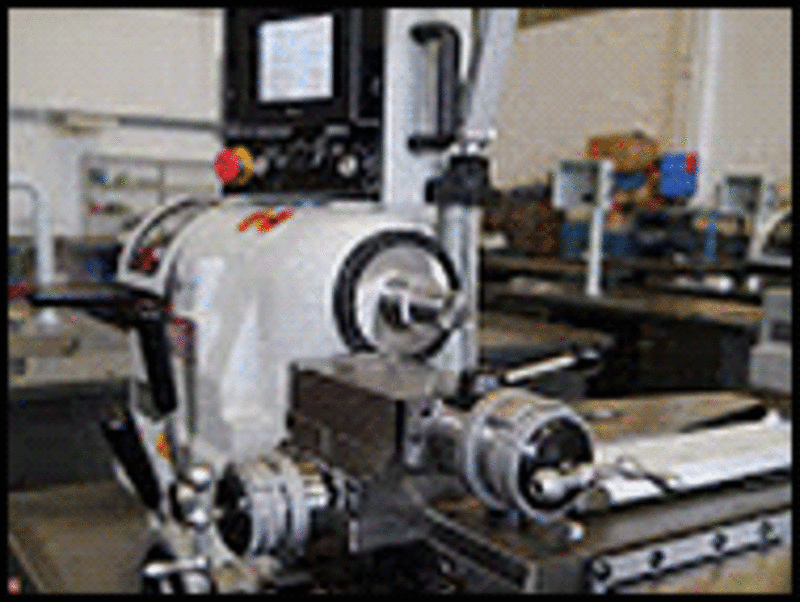
High Speed/high Accurancy Toolroom Lathe With Digital Threading Control Replaces Traditional Threading Gearbox
This lathe doesn't use threading gearbox, instead computer-controlled servo motor is directly linked to the leadscrew. Just use your finger to select desired thread pitch on the touchscreen display, the threads come out absolutely precise and you totally eliminate problems with specialized threads.The disply also shows spindle speed, cutting feed rate and DRO functions.
The First Choice Of Toolmakers!
- Good for pitch and module turning processing without any gears in gearbox. Easy exchange of inch and metric system, accuracy goes up to three degits after decirnal point.
- Digtal data shows R.P.M. of spindle and tool infeed to let operator arrange best possible turning process combination.
- Digtal data showing electric current for easy checking overload turning.
- Rapid retract function is available for shortened pitch module turning processing time.
Control Panel
- The lead screw is driven directly by servo- motor. Through operation of interface, a spindle decoder is used to transfer the motion of lead screw to rectilinear one. The L.C.D touch pad showing the data is applied to control.
- Rapidly returning to the origin is executed according to the principle of temporarily coming off the tracking mode.
- Feeding rate per minute of auto feed is calculated with MODBUS communication protocol interior message data of the converter, so that user s' cutting precision is available much easily and greatly.
【 Metric / Inch Screen 】 【 Digital operation 】 【 Big-character coordinates 】
What is Digital Threading Control?
CTL-618e toolroom lathe with Digital Threading Control replaces traditional threading gearbox with microprocessor-controlled, servo-driven leadscrew. In the past, when a machinst is faced with a workpiece that calls for thread pitch not supported on a conventional lathe, he has to locate and order a custom gear set and take the time to swap out the gears in the gearbox. This is not economically justifiable unless the volume is large enough. CTL-618e toolroom lathe's design eliminates this time-consuming workaround. With the new digital threading system, the user's wishes with it comes to threading can be easily and immediately realized.
Simply type in the desired thread pitch on the numeric keypad on the touch screen LCD control panel and then start the threading cycle as on other conventional lathes. CTL-618e's system would control and synchronize main spindle rotation and Z-axis feed rate to produce precise threading cycle for the given TPI or mm thread pitch.
Besides being able to cut thread pitches not previously available on manual lathes, noise and vibration during threading are also significantly reduced, because there are actually no more gears in the gearbox.
Since CTL-618e already has custom IC and a LCD panel to enable threading control, the next logical step is to integrate DRO functions into it for an all-in-one versatile machine. And CTL-618e has in-fact done that. DRO capabilities are built-in and come standard with no extra charge. CTL-618e features linear scales on X and Z-axis from Mitutoyo.
For people experienced with the super high precision and immediacy of CYCLEMATIC's toolroom lathes, the CTL-618e adds another dimension of capabilities. It builds on the same foundation as 618EVS toolroom lathe. They are all ideal for super high precision lathe work on small parts (usually those that fit in 5C collets). The guaranteed circular accuracy is 50 millionth of an inch.
SPINDLE TOOLING, TOOLING HOLDER AND OPTIONAL EQUIPMENT FOR CYCLEMATIC HIGH SPEED. HIGH ACCURACY TOOLROOM LATHES
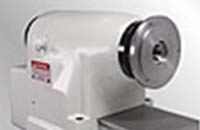
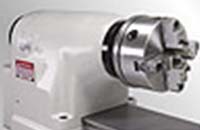
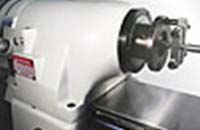
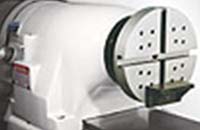
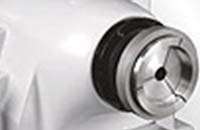
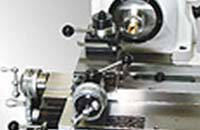
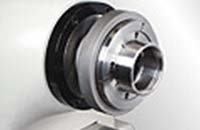
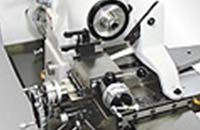
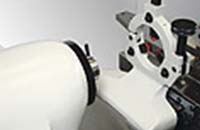
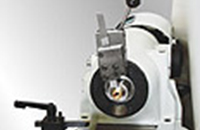
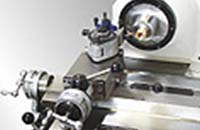
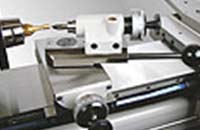
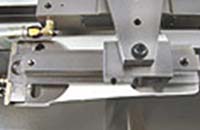
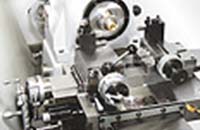
MODEL | CTL-618e | |
---|---|---|
Spindle Capacity | With Chuck | 150 mm (6") |
With Expanding Collets | 76 mm (3") | |
With Round 5C Collets | 27 mm (1-1/16") | |
With Hexagon 5C Collets | 22 mm (7/8") | |
With Square 5C Collets | 19 mm (3/4") | |
With Step Chucks | 27 ~ 152mm (1-1/16-6") | |
Spindle Nose Diameter | Ø55.5 mm (Ø2.189") | |
Spindle Nose I.D/O.D | 5C (10°) / 4° Tapern | |
Spindle Speeds (Variable) | 50-4,000 rpm (5C) / 50-3,000 rpm ( with 6" 3-jaw chuck) | |
Inverter Spindle Motor | 3 HP | |
Hole Through Spindle | 31.75mm (1-1/4") | |
Bar Stock Diameter (5C collet) | Ø27 mm (O1-1/16") | |
Distance Between Centers | 457 mm (18") | |
Swing Over Bed | 280 mm (11") | |
Swing Over Carriage | 230 mm (9") | |
Swing Over Cross Slide | 152 mm (6") | |
Carriage Power Feed Range (Variable) | 8~178 mm (5/16" ~ 7") | |
Cross Slide Power Feed Range (Variable) | 5~102 mm (3/16" ~ 4") | |
Cross Slide Travel | 152 mm (6") | |
Quick-action Compound Slide Travel | 2.5 mm (0.1") | |
Compound Slide Travel | 76 mm (3") | |
Tailstock Spindle Diameter | Ø34.5 mm (1.358") | |
Tailstock Spindle Taper | MT. #2 | |
Tailstock Spindle Travel | 95 mm (3-3/4") | |
Coolant Pump | 1/6 HP. 220V. 3PH | |
Feed Inverter Motor | 1/2 HP | |
Range of Threads | 0.55~6.55 mm (3.175~500 TPI) | |
Main Motor | 3 HP, 220V, 3PH | |
Feed Motor | 110V, 70W | |
Net/Gross Weight | 1,760/1,980 lbs. (800/900 kgs) | |
Machine Packing Dimension | 2,000 x 850 x 1,900 mm (79" x 33" x 75") | |
All dimensions, specifications and machine appearance are subject to change without prior notice. |
CONTENTS:
- PURPOSE OF THIS MANUAL
- LEVEL ADJUSTMENT PROCESS
- LIFTING MACHINE
- A.) INSPECTION AND CLEANING OF MACHINE
- B.) FOUNDATION, INSTALLATION, AND LEVELING
- C.) ELECTRICAL CONNECTIONS
- D.) LUBRICATION
- E.) SPINDLE CONTROL LEVERS
- F.) TOUCH SCREEN GEAR BOX AND HOW TO DOING THE THREADING
- G.) MEMORIZE THE X AND Z POSITION
- H.) AUTOMATIC THREAD LENGTH CONTROL
- I.) SPINDLE BRAKE
- J.) BELT ADJUSTMENT
- K.) COLLET CLOSER-REMOVAL
- L.) COLLET CLOSER-REPLACEMENT
- M.) COLLET CLOSER-ADJUSTMENT
- N.) CARRIAGE INDICATED RING
- O.) CARRIAGE LOCK
- P.) CARRIAGE CLUTCHES
- Q.) CROSS SLIDE INDICATING RING
- R.) QUICK-ACTING TOOL POST COMPOUND SLIDE ASSEMBLY
- S.) POWER FEED UNIT
- T.) COOLANT FACILITIES
- U.) TAILSTOCK
- V.) TAILSTOCK SPINDLE LOCK
- W.) TAILSTOCK BODY LOCK
- OPERATION
PURPOSE OF THIS MANUAL
The model CTL-618e series machine is built for easy and safe operation and excellent manufacturing of work in process. The machine is built with high quality material, and carefully to exacting standards that guarantee the life, economical use, accuracy, and minimum maintenance of the machine.
This manual is an introduction to the CYCLEMATIC model CTL-618e HIGH ACCURACY TOOL ROOM LATHE. It is used for installation, operation and servicing of the CTL-618e CYCLEMATIC MACHINES.
Also, for fast reference, because it is necessary to make minor adjustments or do preventive maintenance. (For personnel and operators who deal with the CTL-618e machine.)
FOR MODEL CTL-618e EQUIPPED WITH ELECTRONIC VARI-SPEED SYSTEM
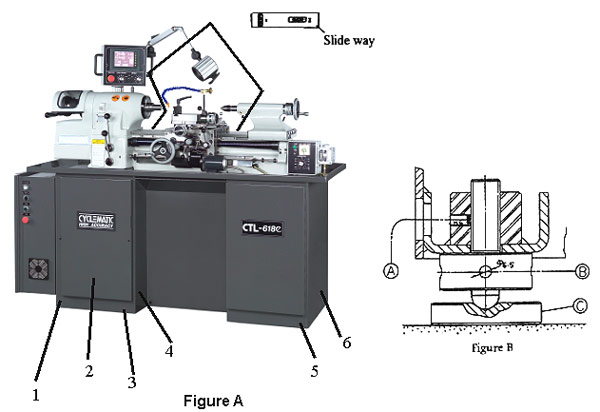
ADJUSTMENT PROCESS FOR LIFTING MACHINE
- Put pads C (Figure B) under each of six points.
- Loose set screw A (Figure B)
- Insert a pin wrench into the hole B. raise or lower by turning (C.W. or C.C.W)
- Tighten set screw A (Figure B) to lock.
- Be sure every point is touching the ground to support the machine.
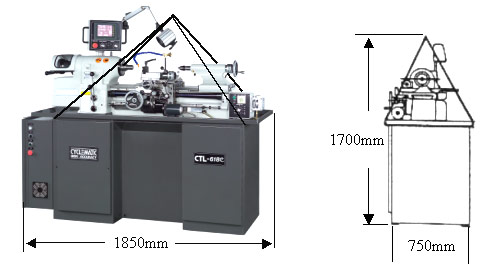
Figure 1 - Lifting machine
Lifting machine, arrange rope or cable as shown in figure 1, and check to see if the correct balance has been obtained. Then insert pads of soft cloth between the edges of the rope and machine. The net weight of this machine is approx 1100 kgs (2420 lbs). So the rope or cable must be rated at 3000 lbs capacity.
A.) INSPECTION AND CLEANING OF MACHINE
An inspection should be made after arrival of the machine in your plant. Look for possible damage caused by shock or vibration during transportation, also check for any missing parts, standard tools or other equipment.
In shipment, all exposed surfaces of the machine are coated with a antirust liquid. Before moving carriage and cross-slide, lead screw, tailstock...etc, these surfaces should be thoroughly cleaned to remove all antirust liquid use a soft brush and solvent. This is very important because it can prevent any dirt or grit which may have accumulated on the antirust liquid from working under the sliding members and causing undue wear.
※ CAUTION:
DO NOT USE COMPRESSED AIR TO CLEAN, WHICH WILL REDUCE THE MACHINES LIFE
B.) FOUNDATION, INSTALLATION, AND LEVELING
A fairly flat foundation and proper installation will provide the machine long-term high accuracy, so supplying a good solid foundation of proper thickness is important. (Generally, a thickness of 300mm (12") is considered to be enough.) The machine has six adjustable feet on the corners of the pedestal base, used for leveling the machine. Place the pads under the feet of pedestal. To adjust, loosen the set screw and raise or lower the foot with a pin wrench so that all six feet rest firmly on the floor. When the adjustment is done, tighten set screws.
C.) ELECTRICAL CONNECTIONS
The CTL-618e TOOLROOM LATHE is shipped completely wired and assembled, Turn Cam Switch "A" (Figure 2) to the "OFF" position, then check motor voltage. Loosen screws "B" (Figure 2), and open the switch case cover, connect the wires from the power source to the terminals (R.S.T), and ground connection is made at the "G" (Figure 3) which is the electric switch case.
Pull out Spindle locking Pin "E" (Figure 4), push "G" (Figure 4) in forward position. The spindle should rotate counterclockwise when viewed from the tailstock end of the machine. If the spindle does not turn in the correct direction, turn Cam Switch "A" (Figure 2) to "OFF" position. Disconnect electric power source, and interchanges any two leads until the turning direction is correct. When the spindle is rotation correctly, secure switch case cover, turn Cam Switch "A" (Figure 2) to "ON" position.
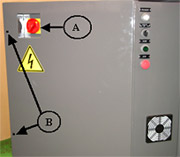
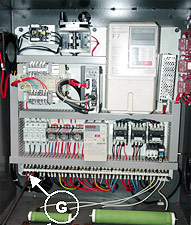
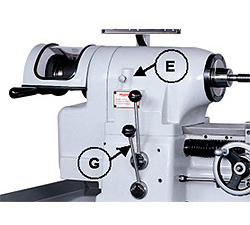
D.) LUBRICATION
Proper lubrication supplied carefully , will maintain the life and performance of the machine for a long period. Therefore, lubricate the machine with a high quality lubricant, and check periodically to assure that the lubricant in the oil sight gage is filled to the proper level.
1. CARRIAGE LUBRICATIONFill with Mobil Vactra Oil No.2 or equivalent in oil reservoir. Lift plunger on reservoir "R" (Figure 5) hold briefly and release to keep bed ways lubricated.

Maintain oil level in sight windows "W" (Figure 7). To fill gearbox, remove plug "C"(Figure 7) use Automatic Transmission Fluid Mobil 200 (Esso ATF or equivalent Change oil every 500 hours).
To drain oil, remove the Drain Plug "M" located under the oil gear box (Figure 7).
※ CAUTION:
USE OF ANY OTHER TYPE OF OIL IN THE GEARBOX MAY
RESULT IN DAMAGE TO THE CLUTCH SURFACES.
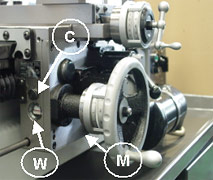
The headstock spindle is mounted on precision preloaded ball bearings. The ball bearings are grease packed for life and require no further lubrication.
E.) SPINDLE CONTROL LEVERS
To change spindle speeds. Push start button "D" (Figure 8). Turn cam switch "C" (Figure 10) to the forward or reverse position and move lever "G" (Figure 9) to the start position. Turn cam switch "D" (Figure 10) right to increase speed or turn left to decrease speed.
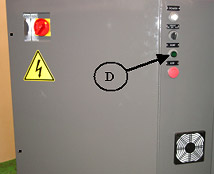
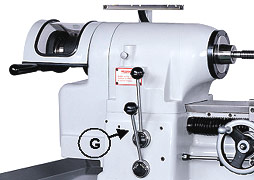

F.) TOUCH SCREEN GEAR BOX AND HOW TO DOING THE THREADING
While you threading, you have to following the steps to set up, first choose the mm/inch set the pitch size by touch screen, and choose the Right hand threador Left hand thread "F" by touch screen, after that choose the pitch "G" (Figure 12) and engage the lead screw nut "J" (Figure 13) by moving ball handled lever "I" (Figure 13) clockwise. Start the spindle by moving the lever "G" (Figure 12). Move the lever "D" (Figure 12 )to make movement going left or right. The threading speed is control by server motor , so if your let the spindle speed faster, the threading speed also will going faster, The rapid speed is control by rapid retract cam "E" (Figure10).
※ CAUTION:
THIS TOUCH SCREEN CAN DOING THE THREADING PITCH
0.01~6.35mm/4~99TPI. (The following speed depends on material)
FOLLOW SPINDLE SPEED LIMIT FOR THREADING OPERATION:
Pitch | 0.05 ~ 1.0mm | 1.001 ~ 2.0mm | 2.01 ~ 4.0mm | 4.001 ~ 6.55mm | 25.001 ~ 550Tpi | 12.001 ~ 25Tpi | 6.501 ~ 12Tpi | 3.175 ~ 6.5Tpi |
---|---|---|---|---|---|---|---|---|
Spindle R.P.M Limit |
3200 | 1600 | 800 | 400 | 3200 | 1600 | 800 | 400 |
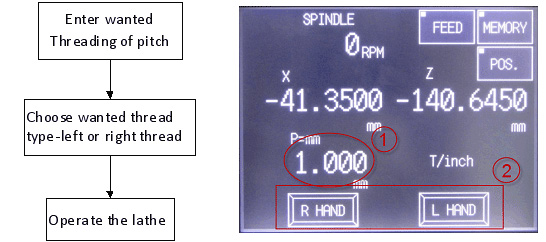
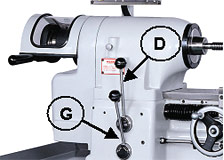
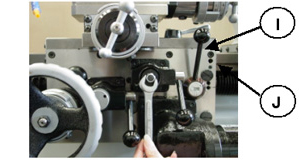
※ CAUTION:
PLEASE FOLLOW TOP OF THREAD CHART , THE SPINDLE SPEED DO NOT OVER SPEED . IF SPINDLE SPEED OVER THE LIMIT , THE TOUCH SCREEN WILL APPEAR "SPINDLE OVER" . ALSO THE THERADING FUNCTION WILL NOT WORK .
G.) MEMORIZE THE X AND Z POSITION
Touch the memory bottom will apper the digital operation system. Touch the SET button before doing any memorize step. If didn't touch set button and memorize key can not be work. Touch the memorize Z and X position. For digital operation have 8 set of memory to memorize the X and Z position. Touch the ▾ switch to 1~4 memory set or 5~8 memory. Touch RETURN to return to the main screen.
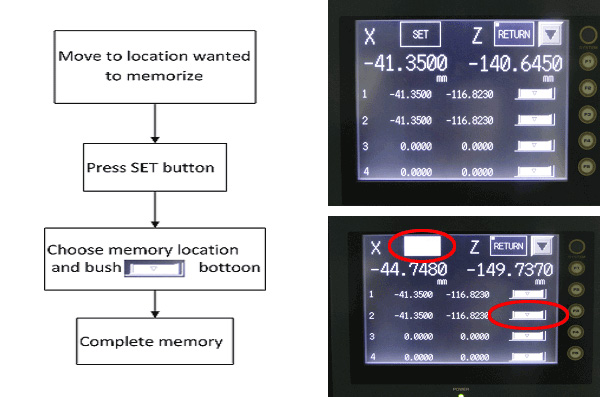
H.) AUTOMATIC THREAD LENGTH CONTROL
When threading into a blind hole or to a shoulder without a thread relief. The lead screw half nut if engaged at the start of the threading work is completed. Left or right hand threads are controlled by Control lever "D" (Figure 18), the lever is joined with the control bar "B" (Figure 19). When the carriage touches the adjusting screw "S" (Figure 19) of the length control bar, it will push the lever "D" (Figure 18) to "STOP" position, and make the lead screw stop.
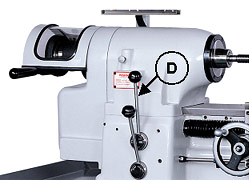
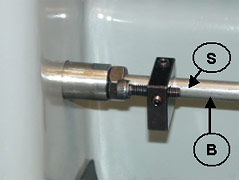
I.) SPINDLE BRAKE
Inverter unit "D" is used to perform dynamic braking. In addition, discharge resister "C" shortens braking time (Figure 20).
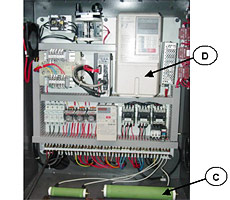
J.) BELT ADJUSTMENT
Run spindle at approximately 1000 rpm. Move lever "G" (Figure 21) to center "STOP" position and let the spindle coast to stop. This is done to equalize belt tension. Loosen lock nut "N" (Figure 22) with 19mm wrench. Turn adjusting screw "P" (Figure22) with screwdriver clockwise to tighten belts. Stop machine and check belt tension, there should be approx.1" of play in belt.
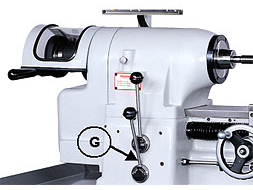
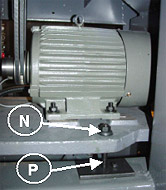
K.) COLLET CLOSER-REMOVAL
Running the machine with the collet closer and not having a collet locked in place will damage the collet closer. Remove the collet closer when using chucks, face plates, or spindle nose type fixtures. The collect closer should be removed often for cleaning to prevent loading of chips between collet closer tube and inside of spindle at rear and collet threads. Removal method is:Pull out pin "L" (Figure 23). Slide draw tube out of the spindle. Do not turn the adjusting nut "N" (Figure 23). It is keyed to the spindle. To remove slide it off the end of the spindle. Do not remove collet closer by removing screw "S" (Figure 23), this screw has been adjusted at the factory for proper operation of the collet closer.
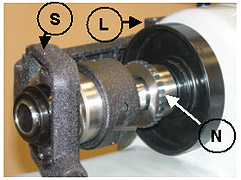
L.) COLLET CLOSER-REPLACEMENT
Before replacement of the closer, clean inside of the headstock spindle and outside diameter at rear of spindle where Adjusting Nut "N" (Figure 24) is located. Apply a film of light oil on rear of spindle Do not force Adjusting Nut "N" on spindle. If Adjusting Nut "N" fits to tight, remove and check for burrs or scratches, then replace. Clean collet closer tube inside and out apply a film of light oil on slip surface "T" (Figure 24) of the collet closer tube, replace collet loser and insert Link Pin "L" (Figure 24).
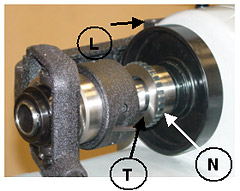
M.) COLLET CLOSER ADJUSTMENT
- Before using collet closer, and any collet or step chuck to be used should be thoroughly cleaned.
- Push the lock Pin "E" (Figure 25). To engage lock pin, turn spindle by hand till lock pin enters notch to lock.
- Press the Closer Adjusting Finger "F" (Figure26) down to the point "P" (Figure 26).
- Guard "G" (Figure 26) forward with the left hand, and hold the collet or stop chuck with the right hand at the same time.
- Place a work piece in collet or step chuck.
- Place lever "L" (Figure 26) to the extreme left fixed position. Turn the Shell Guard "G" (Figure 26) toward operator until the work piece is clamped by the collet.
- Place lever "L" (Figure 26) to the right, the released position. Turn Shell Guard "G" (Figure 26) toward operator, move the Adjusting Finger "F".
Test collet closer's tension on work piece. If the work piece needs additional gripping pressure, press down on the adjusting finger "F" (Figure 26) and turn Shell Guard "G" (Figure 26) forward and lock.
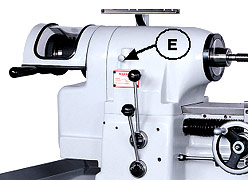
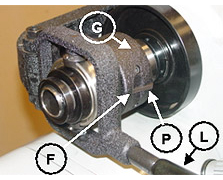
N.) CARRIAGE INDICATED RING
Dual dials with Inch and Metric Hand wheel dial "W" (Figure 27) graduations are in 0.01" 0.2mm. It is built for the operator's convenience of operation. (Figure 28) Spring loaded indicating ring, just turn to required location by loosening lock screw "L" (Figure 27) Sliding cover cage exposes only the dial in use.
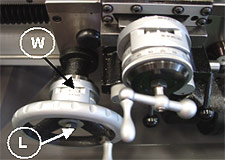
O.) CARRIAGE LOCK
To hold the carriage in a fixed position on the bed use the Carriage Lock Handle "H" (Figure 28). Move the lock handle "H" (Figure 28) clockwise toward the operator, lock the carriage in position. Move the lock handle "H" (Figure 28) counterclockwise away from the operator. To unlock the carriage.
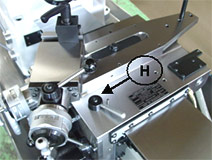
P.) CARRIAGE CLUTCHES
- The carriage clutches are made of a friction type material, designed to slip when slide or carriage engages a feed stop. The clutches are a spring-loaded arrangement and can not be adjusted for more pulling power. If clutch slips under a cut, it is a sign of improper tool grinding, dull tool or excessive feed. The friction clutches have sufficient power to handle all work.
- When the machine contacts a feed "stop", it is intended for the clutch to slip, To operate clutches as shown in (Figure 29), raise handle "H" (Figure 29) approx. 20 degress above horizontal, the clutch will engage, Push down the handle "H" (Figure 29), the clutch will release. When the carriage lead screw is engaged for threading the carriage feed clutch is mechanically interlocked (can not be engaged). This is to prevent machine damage. Adjust clutches as shown in (Figure 29).
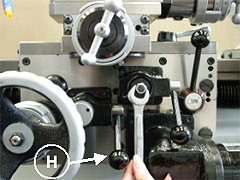
Q.) CROSS SLIDE INDICATING RING
Dual dials with inch and metric hand wheel dial. Each graduation of the Indicating Ring "C" (Figure 30) is 0.02mm (0.001") on the diameter. It is provided for operator's convenience. The Indicating Ring is spring loaded, so a lock screw is not needed. To use it, just turn the Indicating Ring to required location by hand. Cross Slide operation of free and adjustment of clutches are identical with the operation and adjustment of carriage clutches. If CTL-618e TOOLROOM LATHE needs to be used with the taper turning attachment, loosen the screw "S" (Figure 30) with a spanner wrench.
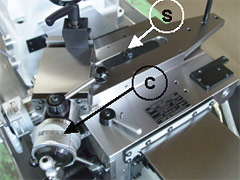
R.) QUICK-ACTING TOOL POST COMPOUND SLIDE ASSEMBLY
The compound slide has a quick-acting tool post, at the start of threading cut, place the ball-handle "H" (Figure 31) of the quick-acting tool post toward the work piece, at the end of the threading cut, the threading tool is instantly cleared from the work by hand operated, handle "H", for the return of the carriage to the next cut, the ball-handle lever actuating the tool post slide feed screw. Operate above procedure repeatedly until the threaded work piece is completed. Each graduation of the indicated ring "C" (Figure 31) is 0.02mm (0.001") on diameter.
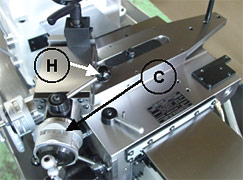
※ CAUTION:
THE BALL-HANDLE LEVER OF THE QUICK-ACTING TOOL POST MUST BE MOVED
TOWARD OPERATOR AT THE END OF THE THREADING CUT.
S.) POWER FEED UNIT
The carriage Power Feed unit is mounted on the carriage.
It is
powered by AC motor "M" (Figure 32).
- The power feed can be operated only when the machine is running. Start the power feed by turning Cam Switch "S" (Figure 33).
- The Cam Switch "S" (Figure 33) controls the direction of the power feed.
- The carriage Feed Control "N" (Figure 33) controls the rate of feed. When Cam Switch "S" (Figure 33) is placed in "RIGHT" position, the carriage will feed toward the right, the cross slide will feed away from the operator.
- When Cam Switch "S" (Figure 33) is placed in "LEFT" position, the carriage will feed toward the left, the cross slide will feed toward operator.
- Turn Cam Switch "S" (Figure 33) to "STOP" position, power feed motor is turned off.
- The rate of the carriage feed should be pre-selected to suit each particular job, which depend on material, diameter, type of cut, and tooling used.
- The numbers on the carriage feed control panel, do not represent either thousandths per revolution or inches per minute. So the operator must test sample pieces for determining the spindle speed and rate of feed which can best suit to the requested surface finish and production rate, then record the proper settings after testing.
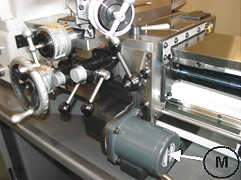
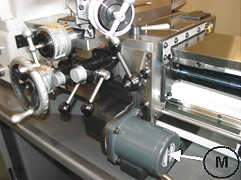
NOTE:
WHEN STARTING INTO PRODUCTION. AN OPERATOR CAN SET THE FEED CONTROL
"N" TO THE RECORDED REFERENCE SETTING, THEN THE SAME TESTED RESULTS
WILL BE OBTAINED.
T.) COOLANT FACILITIES
The coolant pump is controlled by Switch "C" (Figure 34). Turn Switch "C" (Figure 34) to "ON" position, the pump will run continuously, turn to "AUTO" position, the pump will run only when the machine is running. If pump switch is set at "OFF" position, the coolant pump is off. Pump should be cleaned periodically, depending on the type of material being machined.
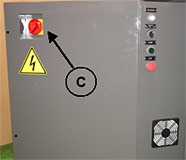
U.) TAILSTOCK
The tailstock is mounted on preloaded ball bearings and can support any load to the spindle. It is provided with a fine "feed" for accurate work. The spindle of the tailstock is graduated in eighths of an inch, and 1 mm and has a travel of 95mm (3-3/4") The hand wheel is dual dial Inch and Metric. Graduations are 0.02mm (0.001"). It is built for the operator's convenience of operation just turn the dial ring "D" (Figure 35) to the required location. It is unnecessary to tighten the dial rings. They are spring loaded, so a lock screw is not needed. Sliding cover cage exposes only the dial in use.
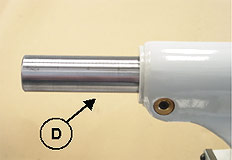
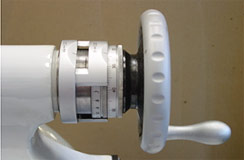
V.) TAILSTOCK SPINDLE LOCK
The tailstock spindle lock holds the spindle securely in any travel position. Move lever "L" (Figure 37) toward the headstock lock position and backward to the released position.
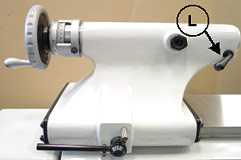
Tailstock Spindle and Body Lock
W.) TAILSTOCK BODY LOCK
The tailstock can be clamped in any position along the bed way by operating Lever "M" (Figure 38). The Lever "M" (Figure 38) should be adjusted to a clamp position between the two stop pins "A" (Figure 38) and "B" (Figure 39). when tailstock is fully clamped, lever "M" (Figure 38) should not contact stop pin "A" (Figure 38).
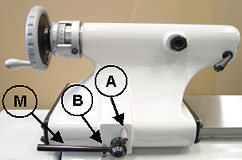
Tailstock Spindle and Body Lock
ITEM | Part no. |
---|---|
1-2 | T-CT-02 |
1-2 | T-CT-03 |
1-2 | T-CT-04 |
1-2 | T-CT-05 |
1-2 | T-CT-06 |
1-2 | T-202-2B |
1-2 | T-202-3B |
1-2 | T-202-4B |
1-2 | T-202-5B |
1-2 | T-202-6B |
1-3 | T-DCT-02 |
1-3 | T-DCT-03 |
1-3 | T-DCT-04 |
1-3 | T-DCT-05 |
1-3 | T-DCT-06 |
1-3 | T-203-2B |
1-3 | T-203-3B |
1-3 | T-203-4B |
1-3 | T-203-5B |
1-3 | T-203-6B |
2-1 | T-SS-1 |
2-1 | T-ES-1 |
2-1 | T-LS-1 |
2-2 | T-UCS-25 |
3-1 | T-CT-01 |
ITEM | Part no. |
---|---|
3-2 | T-304A |
3-2 | T-304B |
3-3 | T-FP-3B |
3-3 | T-FP-5B |
3-3 | T-FP-8B |
3-4 | T-FP-07B |
4-1 | T-317 |
4-1-1 | CHUCK |
4-1-1 | CHUCK |
4-1-1 | CHUCK |
4-1-1 | CHUCK |
4-2 | T-AP-07 |
4-3 | LT-01-109 |
4-4 | LT-01-108C |
5-1 | LT-01-110T |
5-2 | T-315 |
5-2-1 | KM-6 |
5-3 | S-5C |
5-7 | T-3SJ |
7-5 | TDC-6.5 |
7-5 | TDC-10EL |
7-5 | TDC-13EL |
7-5 | TDC-16H |
12-3 | T-KH-48 |
14-1 | 540-110 |
ITEM | Part no. |
---|---|
14-2 | 540-111 |
14-3 | 540-130 |
14-4 | C20-ER20 |
15-2 | TR-303 |
15-3 | T-CLD-618 |
16-2 | T-CSD-618 |
16-3 | T-SR-300 |
16-4 | T-FR-300 |
17-1 | T-LT-01 |
17-2 | T-RT-108 |
17-3 | T-RTS-10 |
18-2 | T-BLD-68 |
18-3 | T-AIT-06 |
21-1 | LB-68-1 |
22-1 | T-CS-10 |
22-2 | T-MC-2 |
22-3 | T-LC-2 |
22-4 | T-DC13-MT2 |
22-4 | T-DC16-MT2 |
22-4 | T-DC19-MT2 |
22-5 | HQ32122-5 |
1-27MM | |
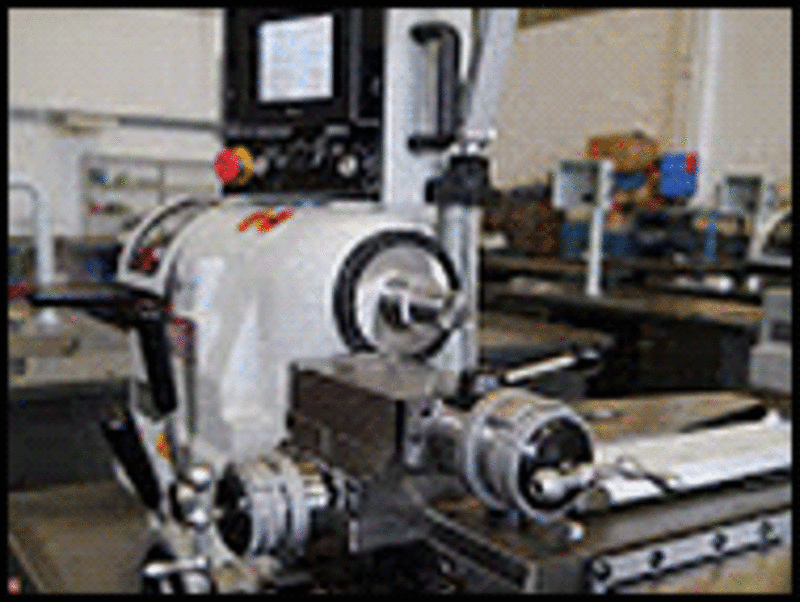
High Speed/high Accurancy Toolroom Lathe With Digital Threading Control Replaces Traditional Threading Gearbox
This lathe doesn't use threading gearbox, instead computer-controlled servo motor is directly linked to the leadscrew. Just use your finger to select desired thread pitch on the touchscreen display, the threads come out absolutely precise and you totally eliminate problems with specialized threads.The disply also shows spindle speed, cutting feed rate and DRO functions.
The First Choice Of Toolmakers!
- Good for pitch and module turning processing without any gears in gearbox. Easy exchange of inch and metric system, accuracy goes up to three degits after decirnal point.
- Digtal data shows R.P.M. of spindle and tool infeed to let operator arrange best possible turning process combination.
- Digtal data showing electric current for easy checking overload turning.
- Rapid retract function is available for shortened pitch module turning processing time.
Control Panel
- The lead screw is driven directly by servo- motor. Through operation of interface, a spindle decoder is used to transfer the motion of lead screw to rectilinear one. The L.C.D touch pad showing the data is applied to control.
- Rapidly returning to the origin is executed according to the principle of temporarily coming off the tracking mode.
- Feeding rate per minute of auto feed is calculated with MODBUS communication protocol interior message data of the converter, so that user s' cutting precision is available much easily and greatly.
【 Metric / Inch Screen 】 【 Digital operation 】 【 Big-character coordinates 】
What is Digital Threading Control?
CTL-618e toolroom lathe with Digital Threading Control replaces traditional threading gearbox with microprocessor-controlled, servo-driven leadscrew. In the past, when a machinst is faced with a workpiece that calls for thread pitch not supported on a conventional lathe, he has to locate and order a custom gear set and take the time to swap out the gears in the gearbox. This is not economically justifiable unless the volume is large enough. CTL-618e toolroom lathe's design eliminates this time-consuming workaround. With the new digital threading system, the user's wishes with it comes to threading can be easily and immediately realized.
Simply type in the desired thread pitch on the numeric keypad on the touch screen LCD control panel and then start the threading cycle as on other conventional lathes. CTL-618e's system would control and synchronize main spindle rotation and Z-axis feed rate to produce precise threading cycle for the given TPI or mm thread pitch.
Besides being able to cut thread pitches not previously available on manual lathes, noise and vibration during threading are also significantly reduced, because there are actually no more gears in the gearbox.
Since CTL-618e already has custom IC and a LCD panel to enable threading control, the next logical step is to integrate DRO functions into it for an all-in-one versatile machine. And CTL-618e has in-fact done that. DRO capabilities are built-in and come standard with no extra charge. CTL-618e features linear scales on X and Z-axis from Mitutoyo.
For people experienced with the super high precision and immediacy of CYCLEMATIC's toolroom lathes, the CTL-618e adds another dimension of capabilities. It builds on the same foundation as 618EVS toolroom lathe. They are all ideal for super high precision lathe work on small parts (usually those that fit in 5C collets). The guaranteed circular accuracy is 50 millionth of an inch.
SPINDLE TOOLING, TOOLING HOLDER AND OPTIONAL EQUIPMENT FOR CYCLEMATIC HIGH SPEED. HIGH ACCURACY TOOLROOM LATHES
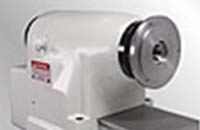
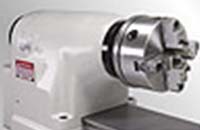
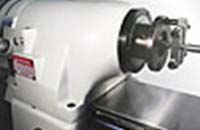
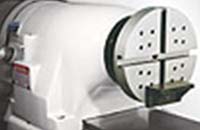
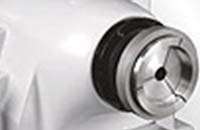
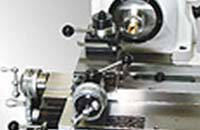
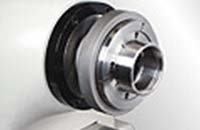
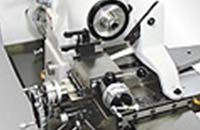
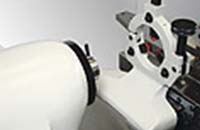
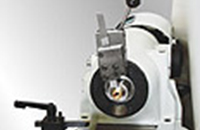
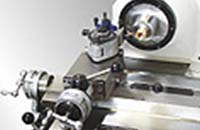
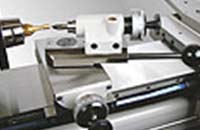
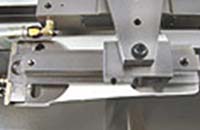
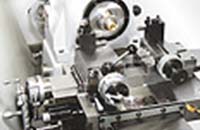