- Guaranteed circular accuracy to 50 millionths of an inch
- Fanuc 0i mate-TF controller(standard), Optional with other brand controller
- Powerful 3 HP motor (5HP-Option) with Yaskawa current vector inverter drive for improved torque response at low end
- Spindle mounted on high precision preloaded angular contact ball bearings
- Precision ballscrew on X and Z axes
- Protection guard on Z-axis ballscrew
- X, Z axes feeds drven by AC servo motor
- X, Z axes ballscrews directly coupled to AC servo motor, minimizing backlash
- Fast lever collect chucking
- Power collet closer
- Optional gang tooling
- Wide variety of accessories to increase versatility
Feature of CNC Lathe Machines
CNC lathe machines use advanced computerized numerically controlled technology to control CNC lathe, it is one of the most advanced and wide ranges of applications types. CNC toolroom lathe has the precise and rapid feature is applicable for the aerospace, automotive, electronics industry, etc. As the lathe machine be published, it not only helps enterprises reduce production and labor costs, reduce mistakes but also increase income and productivity efficiency.
Center turning & gang turning on New CT-1118CNC
CT-1118CNC CNC lathe machine is the NC upgrade from CTL-618EVS manual toolroom lathe. It keeps the original machine's durability and elegant exterior while automating it with servos and CNC control. With CT-1118CNC's 2008 redesign, we go even further, the ability to use tailstock and lathe center to perform shaft work is maintained, but more importantly, an innovative tool plate design adds the capability to remove the compound tool post and swap in T-slot gang tool slide in its place. The gang tool slides great work with a new complete line-up of tool holders from CYCLEMATIC for gang tool turning. Either traditional lathe tooling setup or gang tool setup is easy to swap out and exchange for the other. Now CT-1118CNC is the ONE CNC toolroom lathe that can bring you TWO different styles of machining capability. For more CNC lathe machines detail, just feel free to contact us.
This setup shows the lathe with...
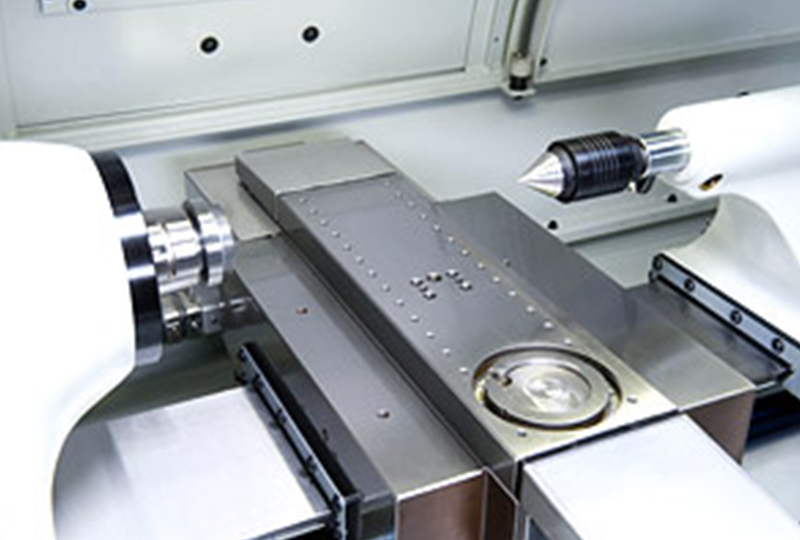
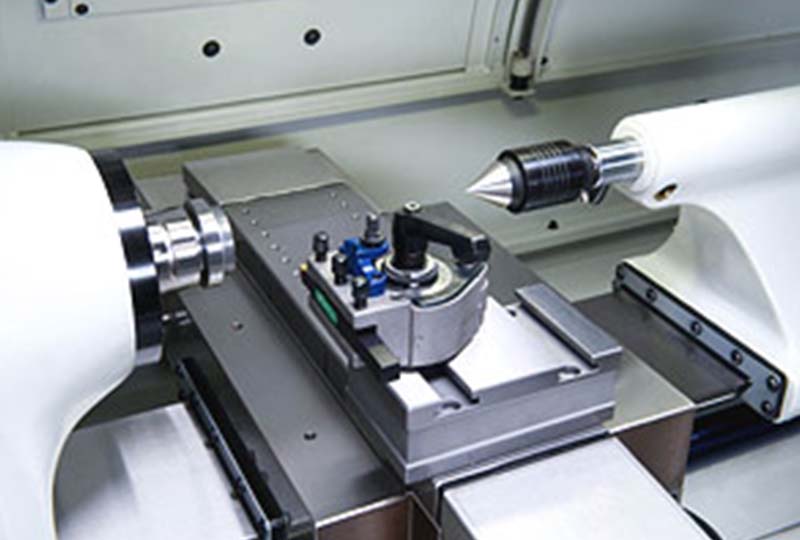
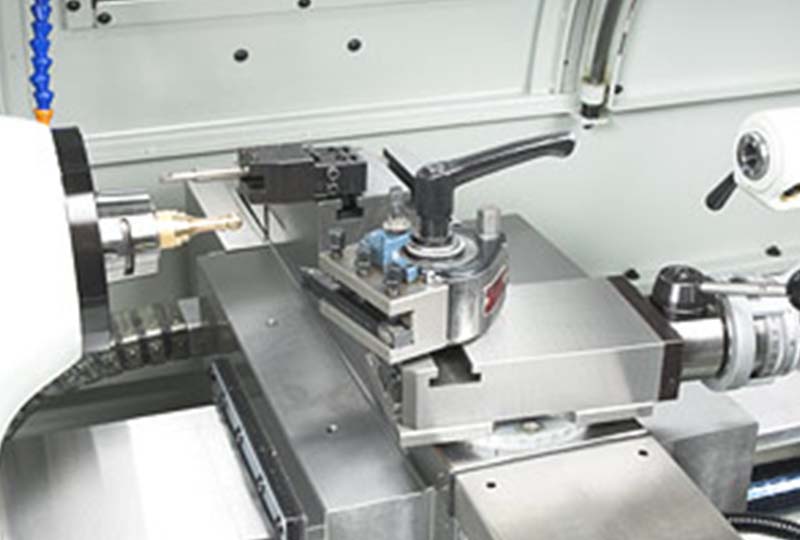
2.Single tool holder in the back
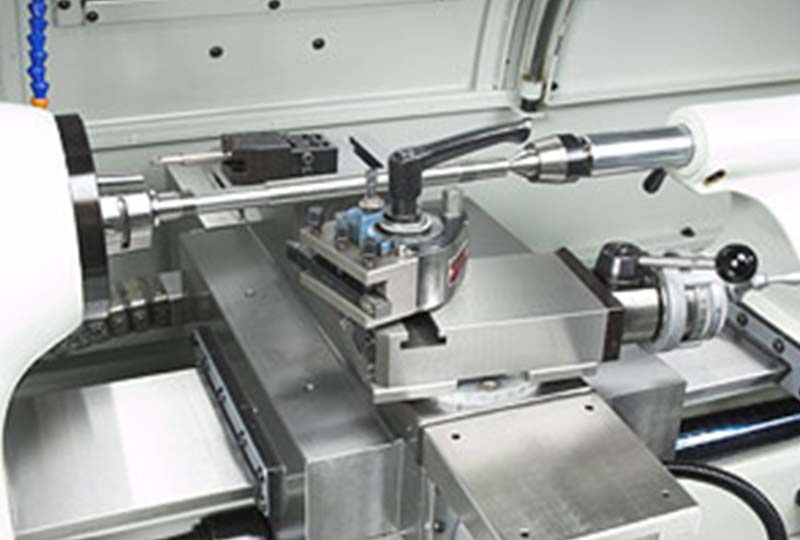
2.Single tool on quick-change tool holder on compound tool slide
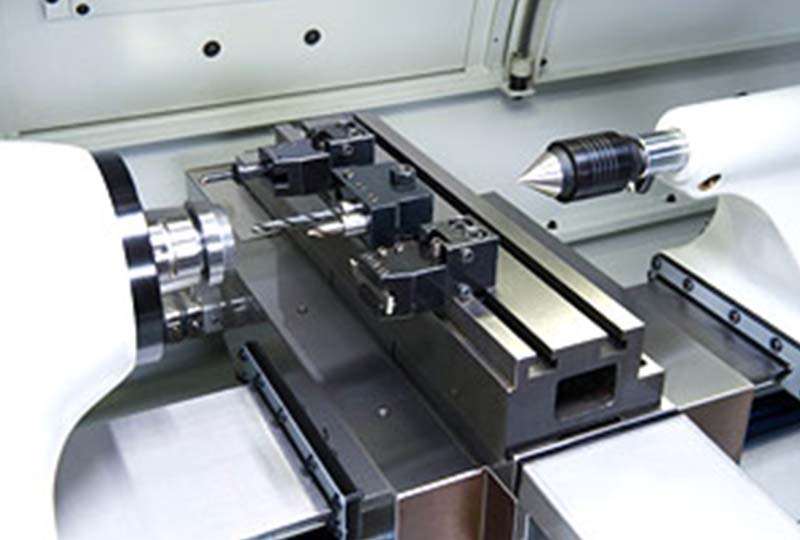
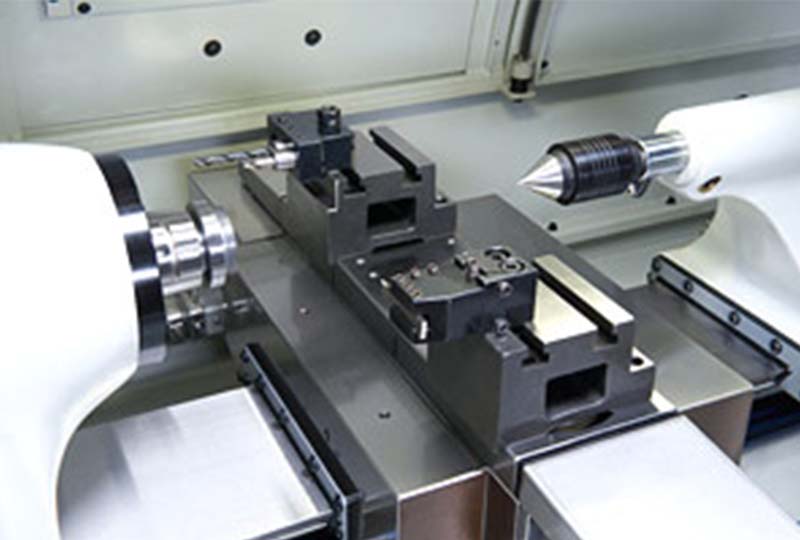
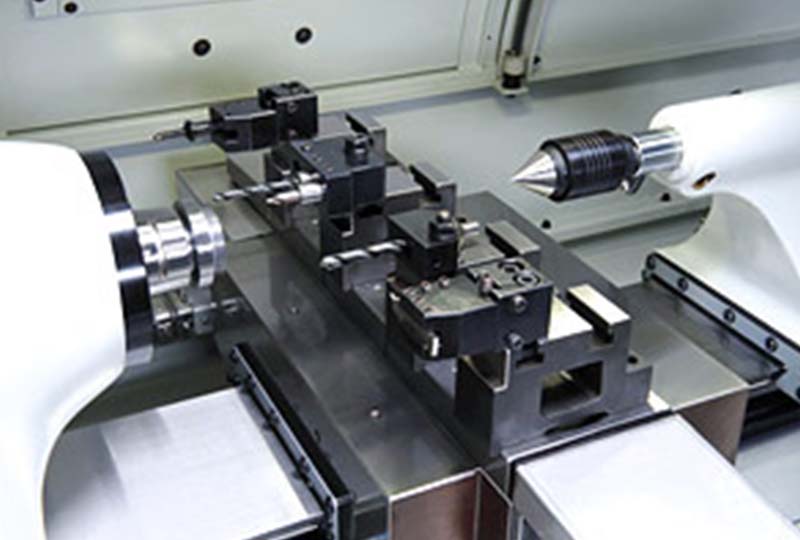
Each holding a single tool holder.
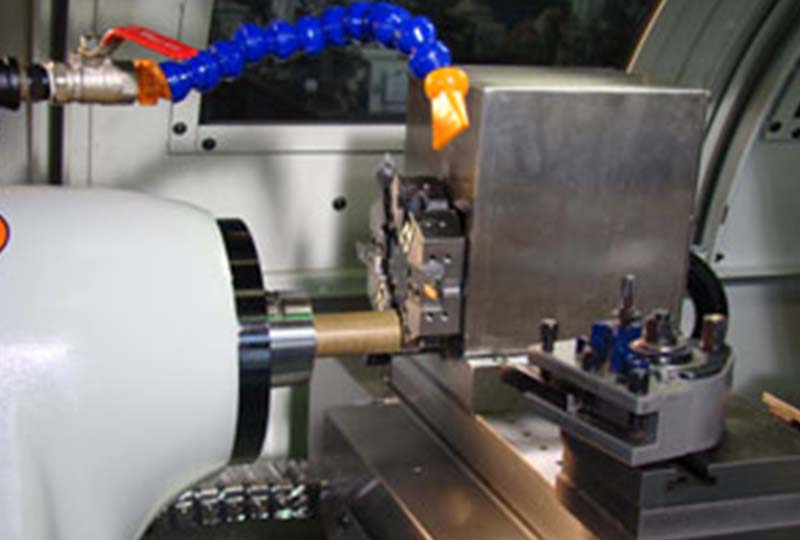
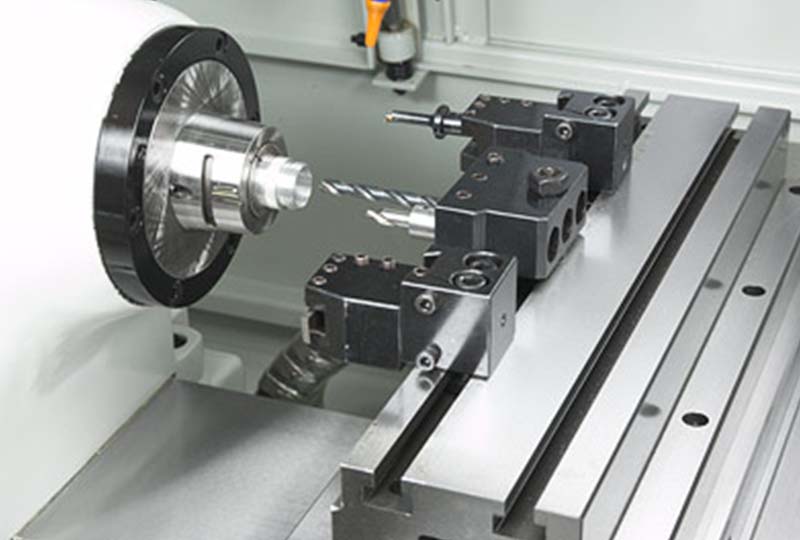
Gang Tooling on CT-1118CNC Toolroom Lathe
There is now one more way to place cutting tools on the CT-1118CNC CNC Toolroom Lathe. Gang tooling makes it easier to setup jobs where multiple tool changes are necessary. It's suitable for higher volume production of the kind of high precision parts toolroom lathes are known for.
SPINDLE TOOLING, TOOLING HOLDER AND OPTIONAL EQUIPMENT FOR CYCLEMATIC HIGH SPEED. HIGH ACCURACY TOOLROOM LATHES
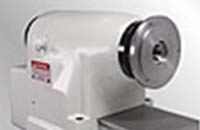
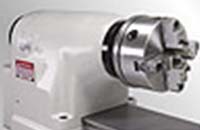
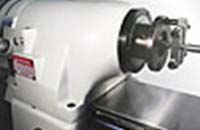
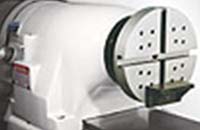
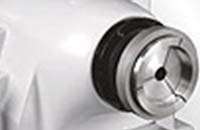
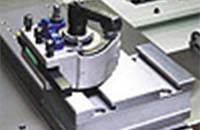
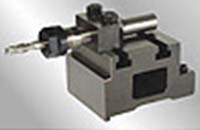
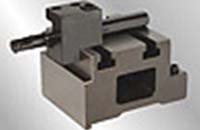
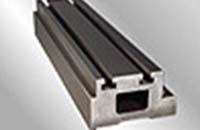
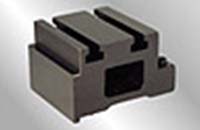
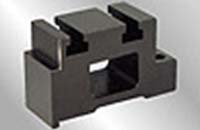
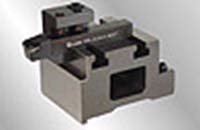
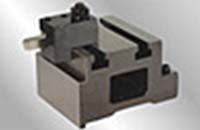
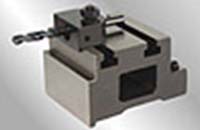
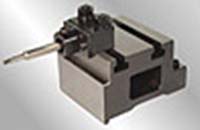
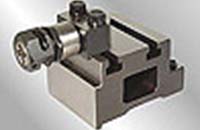
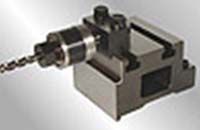
Samples of Matal and Non-Metal Machining
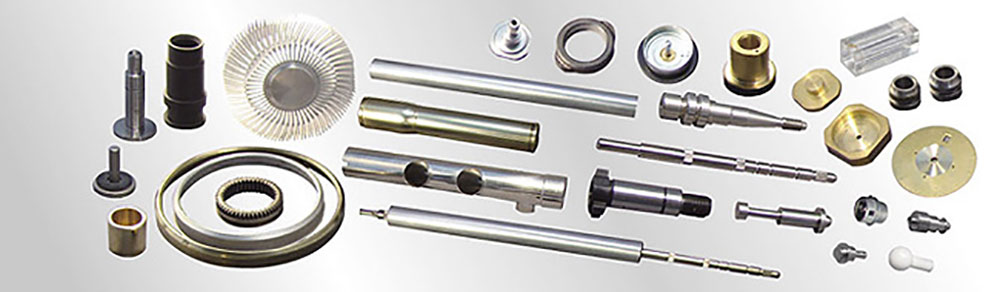
Features
- Guaranteed circular accuracy to 50 millionths of an inch
- Fanuc 0i mate-TF controller(standard), optional with other brand controller
- Powerful 3 HP motor (5HP-Option) with Yaskawa current vector inverter drive for improved torque response at low end
- Spindle mounted on high precision preloaded angular contact ball bearings
- Precision ballscrew on X and Z axes
- Protection guard on Z-axis ballscrew
- X, Z axes feeds drven by AC servo motor
- X, Z axes ballscrews directly coupled to AC servo motor, minimizing backlash
- Fast lever collect chucking
- Power collet closer
- Optional gang tooling
- Wide variety of accessories to increase versatility
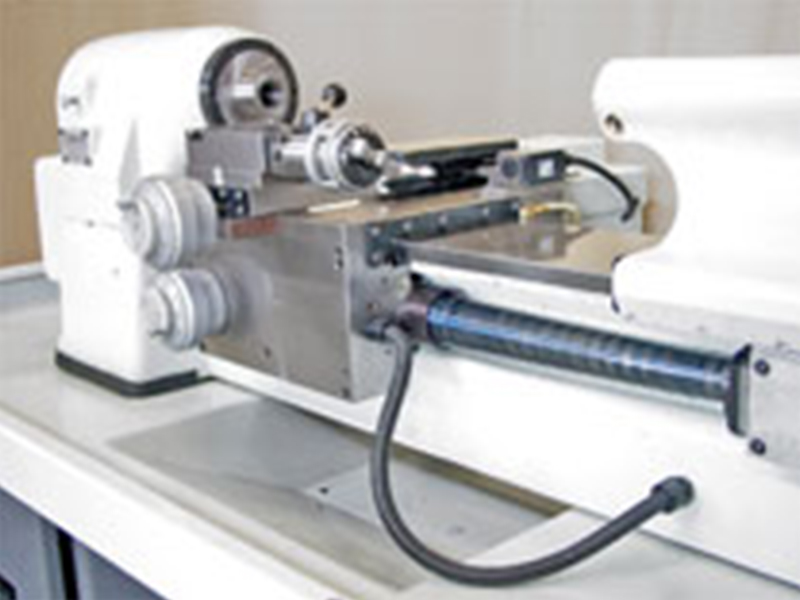
The saddle slideways are coated with Turcite-B for maximum wear resistance.
The cross slideways have hardened and ground tool steel inserts for smooth accurate movement.
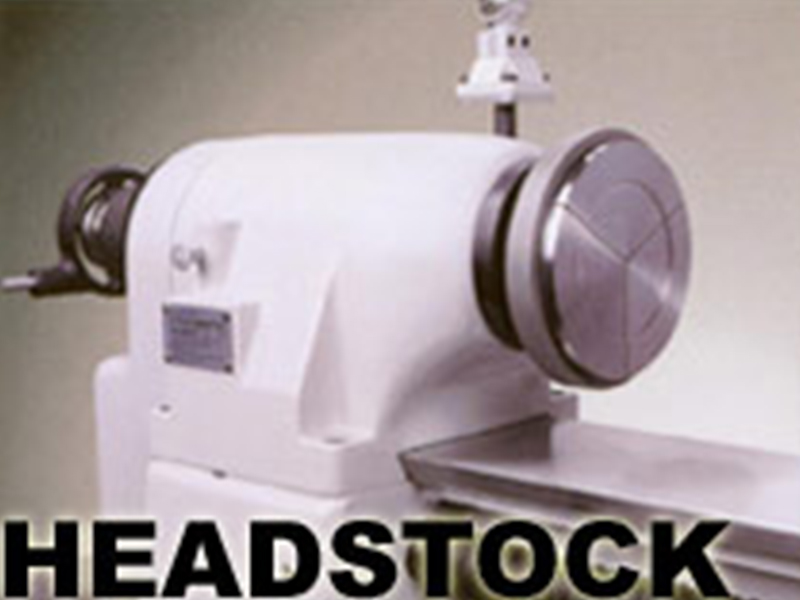
High-precision preloaded ball bearing spindle is mounted in the solid one-piece enclosed
headstock, providing maximum rigidity and sustained precision.
The collet seats directly in the hardened and precision ground
spindle, eliminating troublesome sleeves and adapters that introduce
costly inaccuracies.
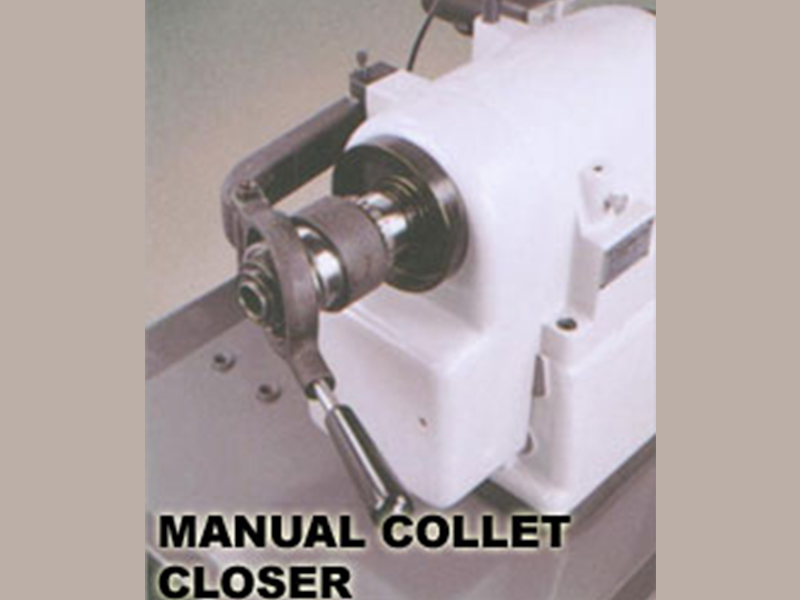
The fast lever collet closer provides faster chucking. The lever
control end of the closer assembly is balanced and rides on a
precision bearing. Collet tension is instantly adjustable throughout
the full range from light to heavy holding power without the use of
tools.
The spindle handwheel is built into the end of the
spindle.
Entire collet closer is conveniently removed by pulling
up the lock pin.
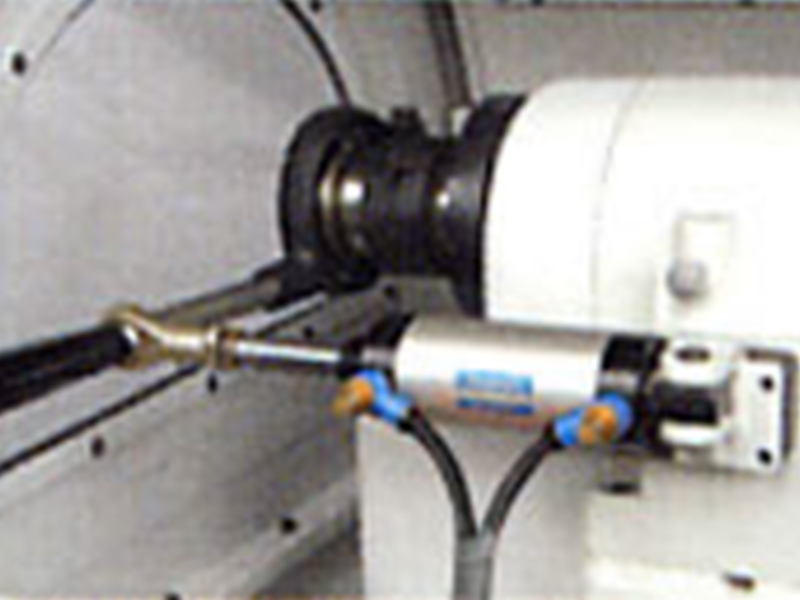
The lathe fit with a easy type power collet closer to replace manual lever operation, this air operated collet closer features automatic chucking.
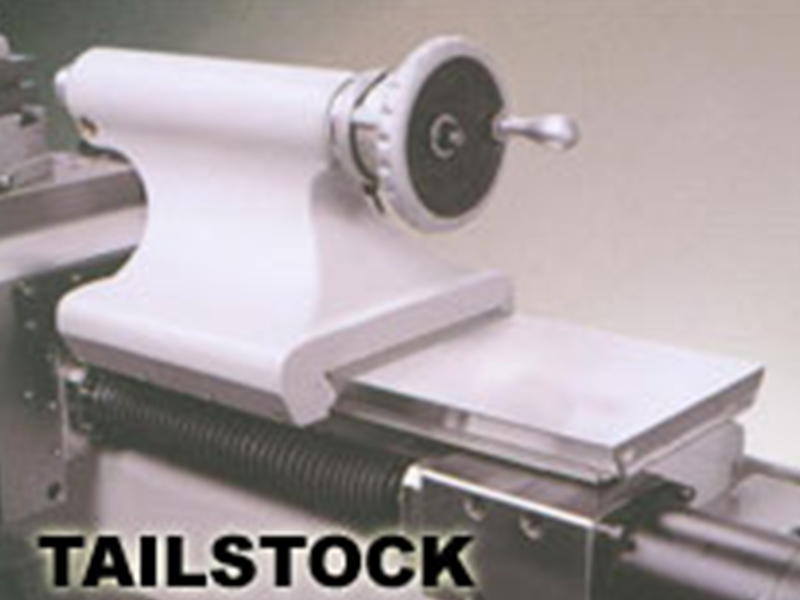
The solid full bearing tailstock supports any load to the preloaded ball bearing spindle headstock, The tailstock has 95mm(3-3/4") travel. The tailstock spindle is graduated in inch and metric for easy reading. Shank of MT#2 taper tools can be automatically discharged for easy operation.
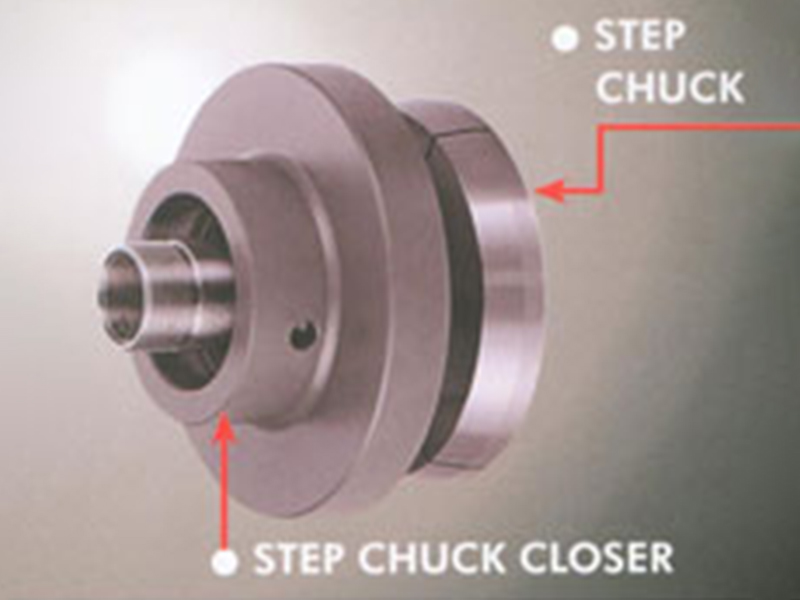
STEP CHUCKS are exceptionally useful for accurately holding work up to 6" in diameter. Castings, moldings, stampings and machined parts are held rigidly and accurately. Tubes can be held without crushing or distorting.
STEP CHUCKS AND CLOSERS are carried in stock in 2", 3", 4", 5" and 6" rated sizes. All step chucks are supplied with pin holes in place for precision machining.
CHUCK CLOSERS fit directly to the machine spindle. A taper corresponding to that on the periphery of the step chuck places the closing pressure over the stepped area of the chuck, resulting in greater gripping power and accuracy.
MODEL | CT-1118CNC |
---|---|
Maximum Swing | 380 mm |
Maximum Turning Diameter | Ø150 mm (O 6") |
Distance Between Centers | 457 mm |
Bar Stock Diameter (5C collet) | Ø27 mm (O1-1/16") |
Hole Through Spindle | Ø31.75mm(O1-1/4") |
CNC Controller | FANUC (STANDARD) |
Spindle Speeds (Variable) | 50~4000 R.P.M. (3HP) / 50~6000 R.P.M. (5HP) |
Spindle Nose I.D./O.D. | 5C (10°) / 4° Taper |
Quick-Action Compound Slide Travel | 2.5 mm (0.1" ) |
Chuck Diameter | Ø150 mm (O6") |
Maximum X-axis Travel | 220 mm (8.661") |
Maximum Z-axis Travel | 340 mm (13.386") |
Rapid Traverse | 20 M/min |
Inverter Spindle Motor | 3 HP / 5HP (Option) |
X, Z-axis Servo Motor | X : s2 / Z : s2 |
Coolant Pump | 1/4 HP |
Tailstock Spindle Taper | MT No.2 |
Tailstock Spindle Travel | 95 mm |
Net/Gross Weight | 2,530/2,750 lb. (1,100/1,200 kg.) |
Machine Packing Dimension | 2,300 x 1,200 x 1,970 mm (91" x 47" x 78") |
All dimensions, specifications and machine appearance are subject to change without prior notice. |
CONTENTS:
- PURPOSE OF THIS MANUAL
- Adjusting process for leveling machine
- A.) ELECTRICAL CONNECTIONS
- B.) LUBRICATION
- C.) COLLET CLOSER REMOVAL
- D.) COLLET CLOSER REPLACEMENT
- E.) COLLET CLOSER ADJUSTMENT
- F.) BELT ADJUSTMENT
- G.) AIR COLLET CLOSER
- H.) AIR F/R.L UNIT
- I.) AUTOMATICALLY OIL PUMP
- J.) FOOT STEP AIR COLLET CLOSER
PURPOSE OF THIS MANUAL
The model CT-1118CNC series CNC toolroom lathe is built for easy and safe operation and excellent manufacturing of work in process. This CNC tool room lathe is built with high-quality material, and carefully to exacting standards that guarantee the life, economical use, accuracy, and minimum maintenance of the machine.
This manual is an introduction to the CYCLEMATIC model CT-1118CNC HIGH ACCURACY CNC TOOL ROOM LATHE. It is used for the installation, operation, and servicing of the CT-1118CNC CYCLEMATIC MACHINES.
Also, for fast reference, because it is necessary to make minor adjustments or do preventive maintenance. (For personnel and operators who deal with the CT-606CNC machine.)
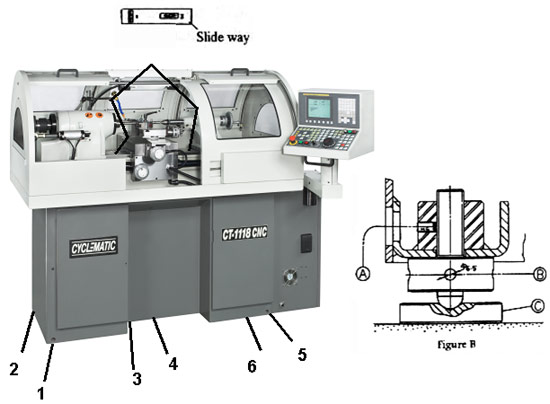
CT-1118CNC
Adjusting process for leveling machine
- Put pads C (Figure B) under each of six points.
- Loose set screw A (Figure B)
- Insert a pin wrench into the hole B. raise or lower by turning (C.W. or C.C.W)
- Tighten set screw A (Figure B) to lock.
- Be sure every point is touching the ground to support the machine.
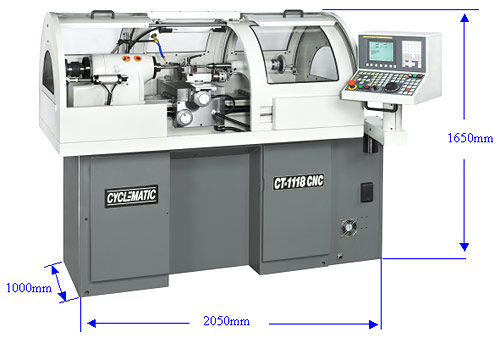
Lifting machine, arrange rope or cable as shown in (Figure C), and check to see if the correct balance has been obtained. Then insert pads of soft cloth between the edges of the rope and machine. The net weight of this machine is approx 1000 kgs (2200 lbs). So the rope or cable must be rated at 3000 lbs capacity.
A.) ELECTRICAL CONNECTIONS
The CT-1118CNC TOOLROOM LATHE is shipped completely wired and assembled. Push the "A" (Figure 1) button, after that, hold handle "B" (Figure 1) and rotate it to the left side. Then turn cam switch "C" (Figure1) to the reverse way, check motor voltage and open the switch case cover, connect the wires from the power source to the terminals (R.S.T) and ground connection is made at the "G" (Figure 2) which is the electric switch case. Push start button to start controller and make spindle run. The spindle should rotate counterclockwise when viewed from the tailstock end of the machine. If the spindle does not turn in the correct direction, turn the machine off. Disconnect electric power source and interchanges any two leads until the turning direction is correct. When the spindle is rotation correctly, secure switch case cover.
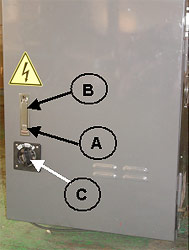
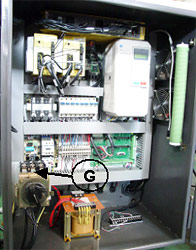
B.) LUBRICATION
Proper lubrication supplied carefully , will maintain the life and performance of the machine for a long period. Therefore, lubricate the machine with a high quality lubricant. Fill with Mobil Vactra Oil No.2 or equivalent in oil reservoir and check oil level usually, please keep oil more then "Min" line (see figure 3).
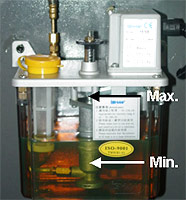
1. HEADSTOCK LUBRICATION
The headstock spindle is
mounted on precision preloaded ball, bearings. The ball bearings are
grease packed for life and require no further lubrication.
2. BALL SCREW LUBRICATION
The ball screw should be
lubricate every month. Please prepare grease gun for lubricate the ball
screw. Before lubricate X-axis ball screw , open screw A (Figure 4) and
fill some grease in to the X-axis ball screw. Fill grease in to the Z-axis
ball screw from B (Figure 5). (The grease can use SUN LIGHT NO.2 or same
kind of grease)
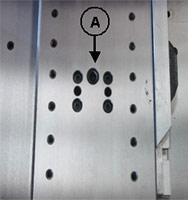
Lubrication
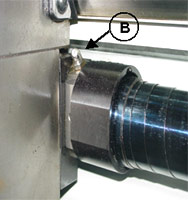
Lubrication
※PLEASE FILL IN SOME GREASE EVERY MONTH. IF NOT, MAY COUSE THE DAMAGE TO MACHINE
C.) COLLET CLOSER REMOVAL
Running the machine with the collet closer and not having a collet locked in place will damage the collet closer. Remove the collet closer when using chucks, face plates, or spindle nose type fixtures. The collet closer should be removed often for cleaning to prevent loading of chips between collet closer tube and inside of spindle at rear and collet threads. Removal method is:Pull out pin "L" (Figure 4). Slide draw tube out of the spindle. Do not turn the adjusting nut "N" (Figure 6). It is keyed to the spindle. To remove slide it off the end of the spindle. Do not remove collet closer by removing screw "S" (Figure 6), this screw has been adjusted at the factory for proper operation of the collet closer.
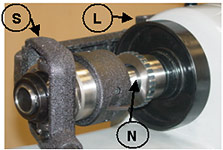
D.) COLLET CLOSER REPLACEMENT
Before replacement of the closer, clean inside of the headstock spindle and outside diameter at rear of spindle where Adjusting Nut "N" (Figure 7) is located. Apply a film of light oil on rear of spindle Do not force Adjusting Nut "N" (Figure 7) on spindle. If Adjusting Nut "N" (Figure 7) fits to tight, remove and check for burrs or scratches, then replace. Clean collet closer tube inside and out apply a film of light oil on slip surface "T" (Figure 7) of the collet closer tube, replace collect loser and insert Link Pin "L" (Figure 7).
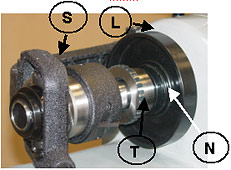
E.) COLLET CLOSER ADJUSTMENT
- Before using collect closer, and any collet or step chuck to be used should be thoroughly cleaned.
- Push the lock Pin "E" (Figure 8). To engage lock pin, turn spindle by hand till lock pin enters notch to lock.
- Press the Closer Adjusting Finger "F" (Figure 9) down to the point "P" (Figure 9).
- Guard "G" (Figure 9) forward with the left hand, and hold the collet or stop chuck with the right hand at the same time.
- Place a work piece in collet or step chuck.
- Place lever "L" (Figure 9) to the extreme left fixed position. Turn the Shell Guard "G" (Figure 9) toward operator until the work piece is clamped by the collet.
- Place lever "L" (Figure 9) to the right, the released position. Turn Shell Guard "G" (Figure 9) toward operator, move the Adjusting Finger "F" (Figure 9).
- Test collet closer's tension on work piece. If the work piece needs additional gripping pressure, press down on the adjusting finger "F" (Figure 9) and turn Shell Guard "G" (Figure 9) forward and lock. (see figure 9).
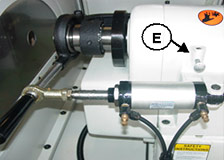
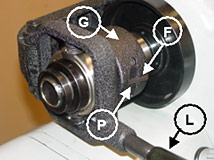
F.) BELT ADJUSTMENT
Run spindle at approximately 1000 rpm and stop the spindle. This is done to equalize belt tension. Loosen lock nut "N" (Figure 10) 19mm wrench. Turn adjusting screw "P" (Figure 10) 6mm socket head wrench clockwise to tighten belts. Stop machine and check belt tension, there should be approx. 25.4mm (1〃) of play in belt.
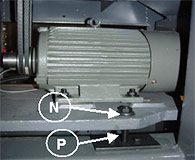
G.) AIR COLLET CLOSER
When collet close, the handle "A" (Figure 11) will go ← way. when collet open, handle "A" (Figure 11) will go → way.
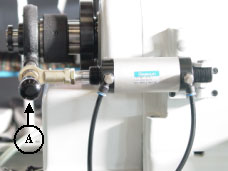
H.) AIR F/R.L UNIT
Air flow in the triangle ➞ on the primary unit. Change psi please pull up 'A' (Figure 12) and counter clock wise it and you may change the psi.
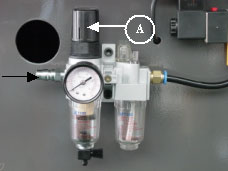
I.) AUTOMATICALLY OIL PUMP
Open 'A'(Figure 11) and fill with Mobil Vactra Oil No.2 or equivalent in oil reservoir when the oil line lower then min line.
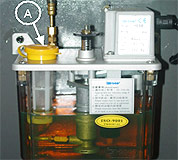
J.) FOOT STEP AIR COLLET CLOSER
Step the foot step air collet closer for open/close collet.
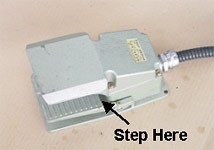
K.) COOLANT TANK
Please fill the coolant water up to max line (Figure 15) , if coolant water less then min line may damage the coolant pump . Change the coolant water , please take off the screw A , the waste water will out of hole.
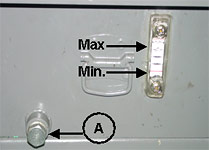
L.) WORK SITUATION LIGHT
When red light shine , it mean machine have some alarm massage or some problem . When yellow light shine , it mean work complete. When green light shine , it mean work is doing right now.
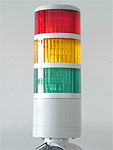
Work situation light
M.) COOLANT
To increase coolant water please push it this way ←. To decrease it goes to this way →.
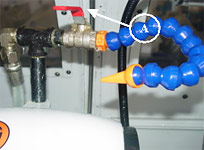
N.) WORKING LAMP (WITH OUT COVER)
Press "LIGHT" key to open or close working lamp.
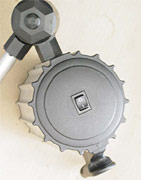
O.) RX232 CONNECTION
CT-1118 CNC Lathe machine have RX232 or CF card to connect with FANUC controller . Also have 110v plug for Note Book.
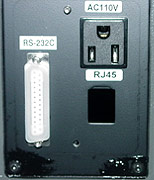
P.) MACHINE SIDE HAND WHEEL
The hand wheel which control Z-Axis is number "1" (Figure 20). For X-axis hand wheel is "2" (Figure 20). If want to use hand wheel in control penal, please punch F1 to decide use machine side hand wheel or control penal side hand wheel.
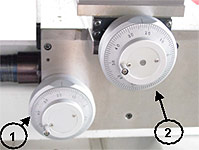
Q.) TAILSTOCK
The tailstock is mounted on preloaded ball bearings and can support any load to the spindle. It is provided with a fine "feed" for accurate work. The spindle of the tailstock is graduated in eighths of an inch, and 1 mm and has a travel of 95mm (3-3/4〃) The hand wheel is dual dial Inch and Metric. Graduations are 0.02mm (0.001〃). It is built for the operator's convenience of operation just turn the dial ring "D" (Figure 22) to the required location. It is unnecessary to tighten the dial rings. They are spring loaded, so a lock screw is not needed. Sliding cover cage exposes only the dial in use.
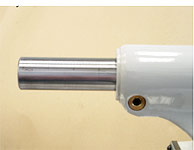
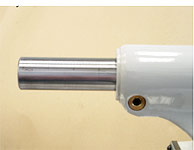
R.) TAILSTOCK SPINDLE LOCK
The tailstock spindle lock holds the spindle securely in any travel position. Move lever "L" (Figure 23) toward the headstock lock position and backward to the released position.
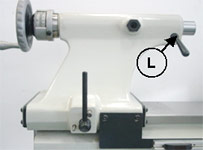
Tailstock Spindle and Body Lock
S.) TAILSTOCK BODY LOCK
The tailstock can be clamped in any position along the bed way by operating Lever "M" (Figure 24). The Lever "M" (Figure 24) should be adjusted to a clamp position between the two stop pins "A" (Figure 24) and "B" (Figure 24). when tailstock is fully clamped, lever "M" (Figure 24) should not contact stop pin "A" (Figure 24).The hard ware limit "N"' (Figure 24) protect the tailstock will not crash with carriage.
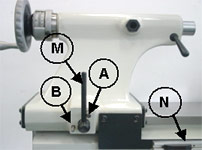
Tailstock Spindle and Body Lock
T.) OPERATING PROCEDURES
Stating procedures:
-
1) Main power switch
- Turn the power of controller on.
- Turn screen power on.
-
2) Machine origin locating
- Press HOME ⑥ and press X ⑦ to return X-axis to origin.
- Press HOME ⑥ and press Z ⑩ to return Z-axis to origin.
※EXECUTE MACHINE ORIGIN LOCATING WHENEVER THE MACHINE STARTS, OR ERRORS WILL OCCUR AND PROGRAM CAN NOT BE EXECUTED AFTER WARDS.
- 3) Perform daily job.
U.) TEST THE ROTATING DIRECTION OF SPINDLE
- Switch on main power switch.
- Turn the power of controller on.
- Press MDI ③ , key in M3 S100 ; and press insert and press cycle start Ⓒ.
- Rotate ↺ way (clockwise).
※THE SPINDLE SHALL ROTATE IN THE DIRECTION OF AN ARROW WAY, WHICH IS SHOWING IN THE VICINITY OF THE SPINDLE. IF THE SPINDLE IS ROTATING IN THE OPPOSITE DIRECTION, PLEASE TURN OFF POWER AND OPEN ELECTRICAL BOX AND SWITCH ANY 2 WIRED, AFTER THAT THE SPINDLE SHOULD BE ROTATE CORRECT WAY.
V.) STANDARD FUNCTION
A) POWER OFF:
Button for power off CNC
controller.
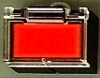
B) POWER ON:
Button for power on CNC
controller.
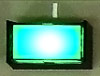
C) CYCLE START:
Button for cycle start the
program.
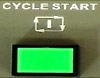
D) FEED HOLD:
Button for hold feed rate or stop machine moving.
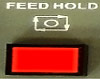
E) FEED RATE CONTROL:
Switch for feed rate
percentage.
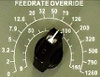
F) PANEL HAND WHEEL:
Turn the switch for X and
Z axis, X1= move 0.001 MM, X10 = move 0.01 MM, X100 = move 0.1 MM. (
If order machine side hand wheel, use F1 to switch standard hand wheel
or machine side hand wheel ) .
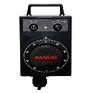
G) EMERGENCY STOP:
For any emergency condition, press the button to stop all the moving elements immediately.
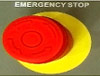
1) DNC:
Use RS232C connect with PC. sometimes file too big to save into the FANUC controller, use
DNC to transfer file also doing the work in same time.
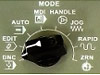
2) EDIT:
Edit program file to the FANUC
controller.
3) AUTO:
Select the AUTO +
CYCLE START button for run the program.
4) MDI:
Select the MDI for edit
short machine code or one time program edit, after press cycle start
those code or program file will disappear(For more info please see Fanuc
operator's manual) ps. Change Fanuc parameter should be in MDI mode,
otherwise it won't effect.
5) HANDLE:
Select the HANDLE for
use hand wheel . For panel side hand wheel can select x or z axis . ( If
customer order machine side hand wheel , use F1 to switch panel side
hand wheel or machine side hand wheel .)
6) JOG:
Select the JOG move X or
Z axis, for use this function please select JOG and
press
,
,
,
to move any direction of axis.
(For more info please see Fanuc
operator's manual) also change feed rate control can be change the
JOG speed.
7) RAPID:
Select the RAPID to
fast move X or Z axis , for use rapid function please select
RAPID and press
,
,
,
to move any direction of axis .
8) ZRN:
Select the ZRN to return
the X and Z axis origin, for use this function Select
ZRN
+
after X axis return to origin then press
to return Z axis origin. (ps. use×1, ×10, ×100, ×1000 can be control
HOME speed, recommend use×10 to HOME).
9) POSITIVE OF X AXIS:
To use with
JOG , RAPID , ZRN.

10) NEGATIVE OF X AXIS:
To use with
JOG , RAPID , ZRN.

11) NEGATIVE OF Z AXIS:
To use with
JOG , RAPID , ZRN.

12) POSITIVE OF Z AXIS:
To use with
JOG , RAPID , ZRN.

13) SPECIAL FUNCTION F1:
Use
key to switch machine hand wheel or penal and wheel.

14) OT RELEASE:
Axis is over travel to hardware
limited switch, push the button for release the error, then move axis
back by JOG or RAPID.

15) SINGLE BLOCK:
Use this function for running
program by single block, if want to move on next line, have to press
cycle start every time.

16) OPITIONAL STOP:
Use this function for optional stop the program. Light's on, when program read to Mo1, machine will stop, need press cycle start to let program continue.

17) WORK LAMP ON/OFF:
Press the key to turn
on/off the working lamp.
Ps. When lamp lights on mean's light will
on

18) BLOCK SKIP:
Use this function for block skip
program. When front of machine code add / , also the block skip light
are on , it's mean controller will skip this code line .

19) DRY RUN:
Use this function for dry run
machine, ignore any feed rate.

20) MACHINE LOCK:
Use this function for lock
machine, only run the program, machine did not move. after use machine
lock, must HOME again. If not may cause machine damage . Use this
function for lock machine, only run the program, machine did not move.

21) COOLANT AUTO:
Use this function for auto
coolant, use M8、M9 code to open/close coolant pump.

22) COOLANT ON:
Use this function for manual
coolant pump, press button to open/close coolant pump.

23) PROGRAM EDIT LOCK :
To lock the edit program,
make people can't program the code by edit or change it.

24) RAPID TRAVERSE OVERRIDE:
This selection use
for rapid low speed. Also home speed can control.

25) RAPID TRAVERSE OVERRIDE 25%:
This selection
use for rapid 25% speed. also home speed can control, (recommend use
this speed to home.)
26) RAPID TRAVERSE OVERRIDE 50%:
This selection
use for rapid 50% speed. also home speed can control.
27) RAPID TRAVERSE OVERRIDE 100%:
This selection
use for rapid 100% speed.
28) SPINDLE SPEED OVERRIDE:
This selection use
for decrease spindle speed or increase spindle speed . Normally this
selection will select at 100% .

29) CLOCKWISE SPINDLE:
This button use for clockwise spindle, when light on telling you spindle clockwise right now. (For lathe machine clockwise spindle should go ↺ way when you stand front of machine).

30) STOP SPINDLE:
This button use for stop spindle.

31) COUNTER CLOCKWISE SPINDLE:
This button use
for counter clockwise spindle, when light on telling you spindle is
counter clockwise right now.

32) JOG SPINDLE:
This button use for jog the
spindle when you press this button spindle will goes really slowly by
clockwise.

33) LUBE ALARM:
When light on, it mean out of oil
and please fill some oil into the cub.

34) NC ALARM:
When light on, it mean the CNC have
some problem, press penal key to read massage after
finish reading, press reset to remove massage and light.

35) MOTOR ALARM:
When left corner red light on,
it mean the motor have some problem , please check it.

36) CHUCK CLOSE:
When light on, it mean chuck is
close, if light not flash on, it mean chuck is open . when chuck open
you can't rotate the spindle.

37) TURRET: Optional Unit
This function key can
manual change tool.

38) X AXIS HOME:
When light on , it mean X axis
has been home. After move x axis the light will off .

39) Z AXIS HOME:
When light on , it mean Z axis
has been home. After move Z axis the light will off .

ITEM | Part no. |
---|---|
1-2 | T-CT-02 |
1-2 | T-CT-03 |
1-2 | T-CT-04 |
1-2 | T-CT-05 |
1-2 | T-CT-06 |
1-2 | T-202-2B |
1-2 | T-202-3B |
1-2 | T-202-4B |
1-2 | T-202-5B |
1-2 | T-202-6B |
1-3 | T-DCT-02 |
1-3 | T-DCT-03 |
1-3 | T-DCT-04 |
1-3 | T-DCT-05 |
1-3 | T-DCT-06 |
1-3 | T-203-2B |
1-3 | T-203-3B |
1-3 | T-203-4B |
1-3 | T-203-5B |
1-3 | T-203-6B |
2-1 | T-SS-1 |
2-1 | T-ES-1 |
2-1 | T-LS-1 |
2-2 | T-UCS-25 |
3-1 | T-CT-01 |
3-2 | T-304A |
3-2 | T-304B |
3-3 | T-FP-3B |
3-3 | T-FP-5B |
3-3 | T-FP-8B |
3-4 | T-FP-07B |
4-1 | T-317 |
4-1-1 | CHUCK |
4-1-1 | CHUCK |
4-1-1 | CHUCK |
ITEM | Part no. |
---|---|
4-1-1 | CHUCK |
4-2 | T-AP-07 |
4-3 | LT-01-109 |
4-4 | LT-01-108C |
5-1 | LT-01-110T |
5-2 | T-315 |
5-2-1 | KM-6 |
5-3 | S-5C |
5-4 | TF-3B-4 |
5-5 | CA5-25 |
5-6 | PA6-100 |
5-7 | T-3SJ |
6-1 | TH-01 |
6-2 | TH-02 |
6-3 | TH-03 |
6-4 | TH-04R |
6-4 | TH-04L |
7-1 | TH-04A |
7-2 | TH-05 |
7-3 | TH-06 |
7-4 | TH-07-1 |
7-4 | TH-07-2 |
7-4 | TH-07-3 |
7-4 | TH-07-4 |
7-5 | TDC-6.5 |
7-5 | TDC-10EL |
7-5 | TDC-13EL |
7-5 | TDC-16H |
8-1 | TH-42 |
8-1 | TH-43 |
8-2 | TH-44 |
8-2 | TH-45 |
8-3 | T-QC-12 |
8-4 | TH-48 |
8-4 | TH-49 |
ITEM | Part no. |
---|---|
8-4 | TH-50 |
8-4 | TH-51 |
9-1 | T-AH-10 |
9-2 | T-RT-16C |
9-3 | T-RT-16 |
9-4 | T-KT-16 |
10-3 | T-BT-3 |
10-4 | T-BT-6 |
11-1 | T-CFT-16 |
11-2 | T-RT-08 |
11-3 | T-RRD-05 |
11-4 | T-SL-408 |
12-1 | T-SL-96 |
12-2 | T-SL-48 |
12-3 | T-KH-48 |
13-1 | T-HE-16 |
13-2 | T-RS-201 |
13-3 | T-ST-10 |
14-1 | 540-110 |
14-2 | 540-111 |
14-3 | 540-130 |
14-4 | C20-ER20 |
15-2 | TR-302 |
16-3 | T-SR-300 |
16-4 | T-FR-300 |
18-3 | T-AIT-06 |
21-1 | LB-68-1 |
22-2 | T-MC-2 |
22-3 | T-LC-2 |
22-4 | T-DC13-MT2 |
22-4 | T-DC16-MT2 |
22-4 | T-DC19-MT2 |
1-27MM | |
Feature of CNC Lathe Machines
CNC lathe machines use advanced computerized numerically controlled technology to control CNC lathe, it is one of the most advanced and wide ranges of applications types. CNC toolroom lathe has the precise and rapid feature is applicable for the aerospace, automotive, electronics industry, etc. As the lathe machine be published, it not only helps enterprises reduce production and labor costs, reduce mistakes but also increase income and productivity efficiency.
Center turning & gang turning on New CT-1118CNC
CT-1118CNC CNC lathe machine is the NC upgrade from CTL-618EVS manual toolroom lathe. It keeps the original machine's durability and elegant exterior while automating it with servos and CNC control. With CT-1118CNC's 2008 redesign, we go even further, the ability to use tailstock and lathe center to perform shaft work is maintained, but more importantly, an innovative tool plate design adds the capability to remove the compound tool post and swap in T-slot gang tool slide in its place. The gang tool slides great work with a new complete line-up of tool holders from CYCLEMATIC for gang tool turning. Either traditional lathe tooling setup or gang tool setup is easy to swap out and exchange for the other. Now CT-1118CNC is the ONE CNC toolroom lathe that can bring you TWO different styles of machining capability. For more CNC lathe machines detail, just feel free to contact us.
This setup shows the lathe with...
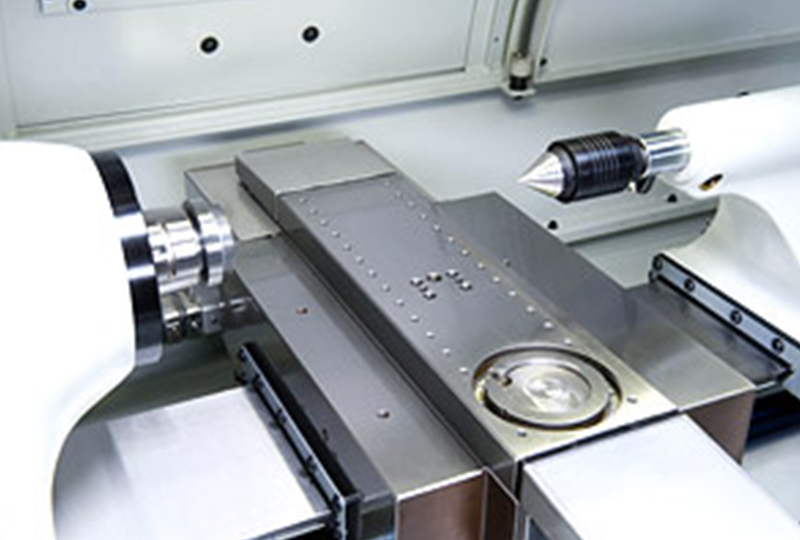
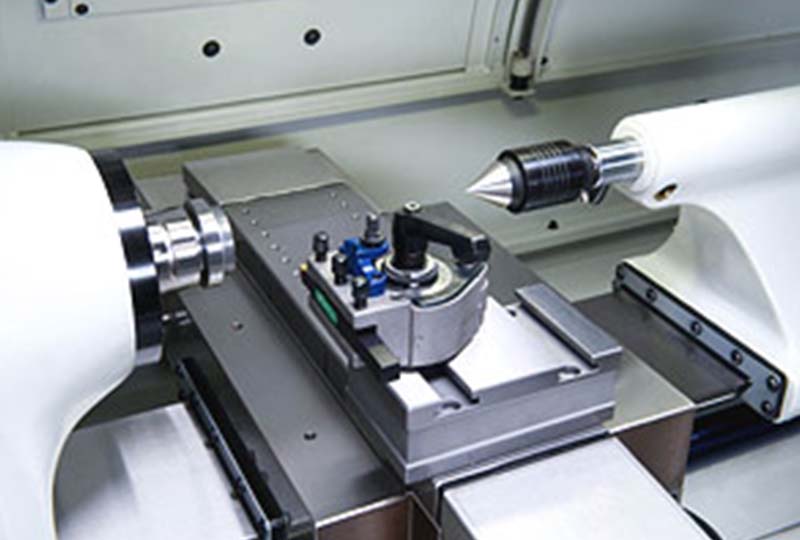
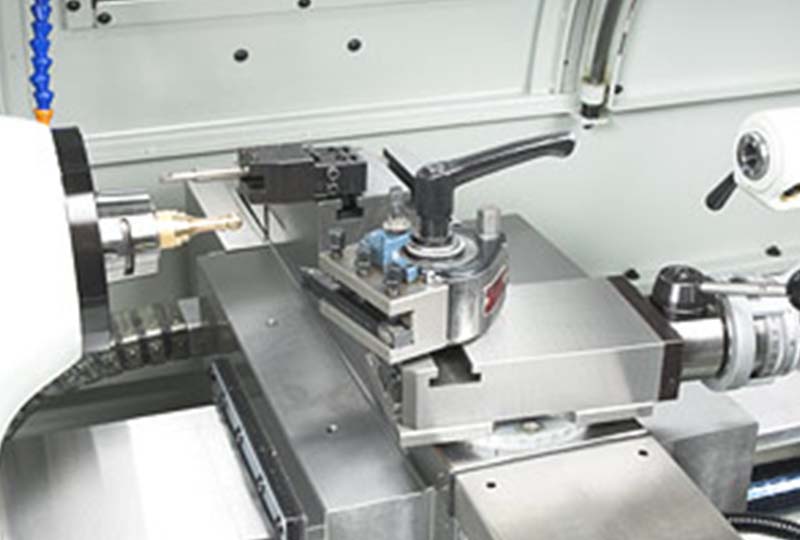
2.Single tool holder in the back
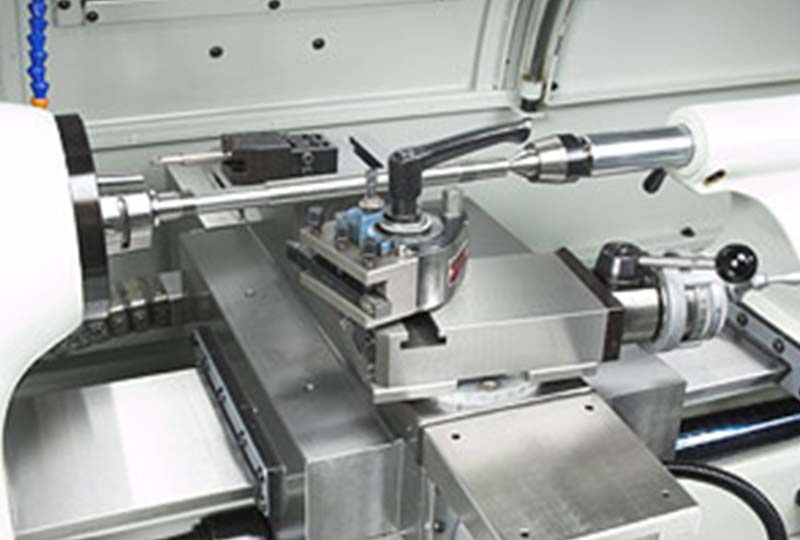
2.Single tool on quick-change tool holder on compound tool slide
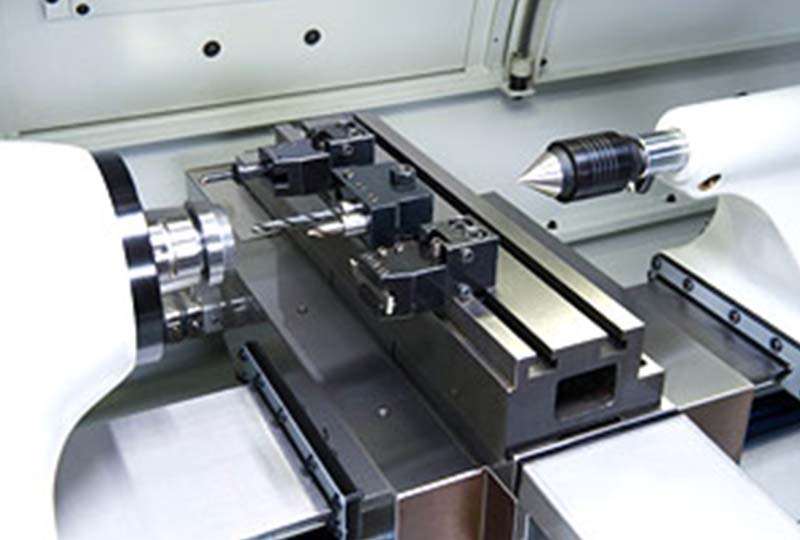
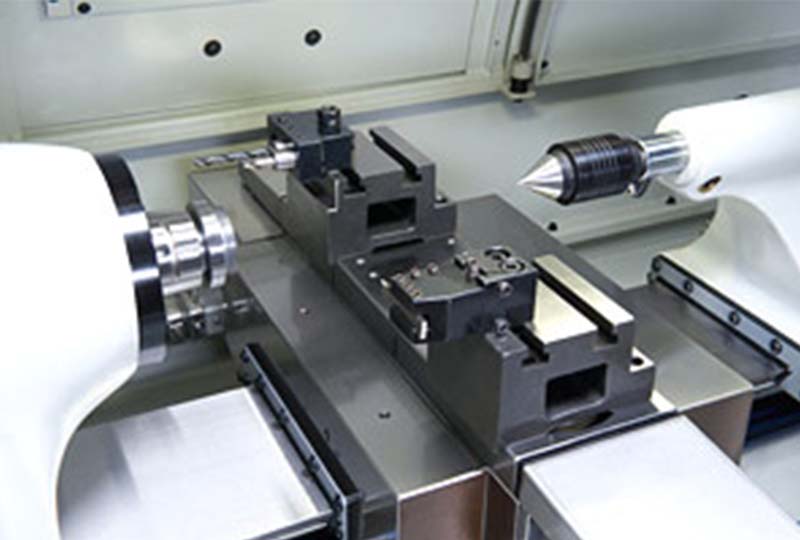
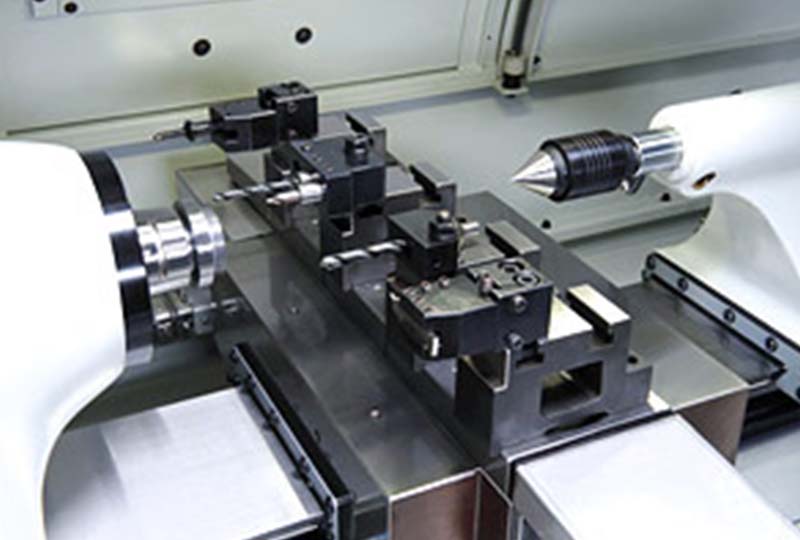
Each holding a single tool holder.
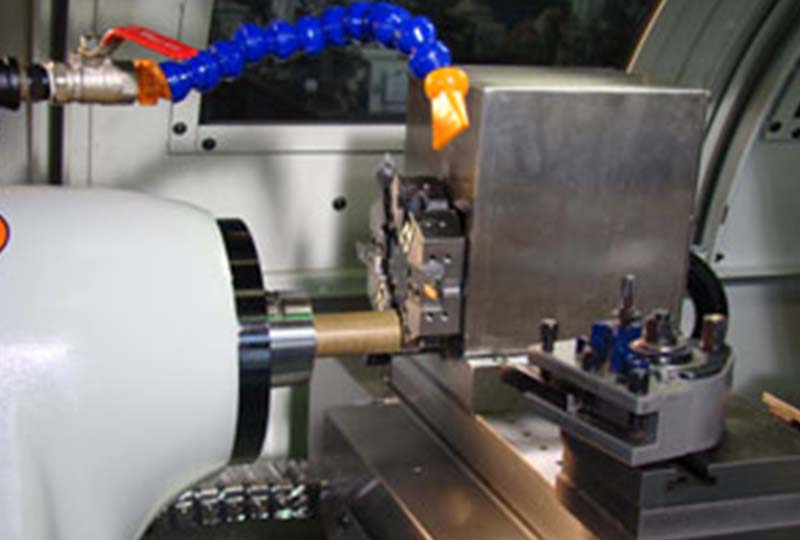
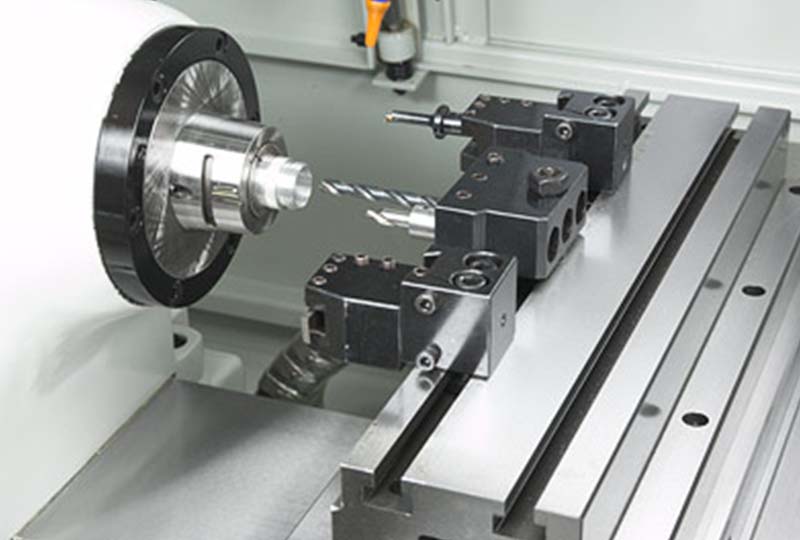
Gang Tooling on CT-1118CNC Toolroom Lathe
There is now one more way to place cutting tools on the CT-1118CNC CNC Toolroom Lathe. Gang tooling makes it easier to setup jobs where multiple tool changes are necessary. It's suitable for higher volume production of the kind of high precision parts toolroom lathes are known for.
SPINDLE TOOLING, TOOLING HOLDER AND OPTIONAL EQUIPMENT FOR CYCLEMATIC HIGH SPEED. HIGH ACCURACY TOOLROOM LATHES
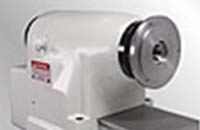
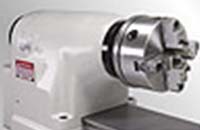
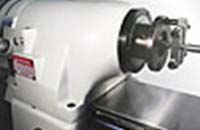
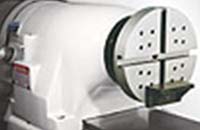
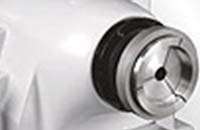
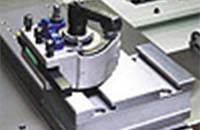
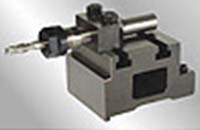
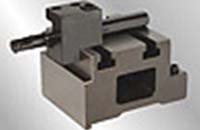
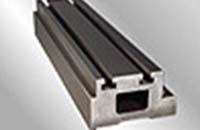
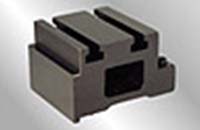
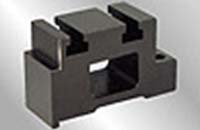
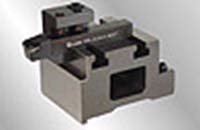
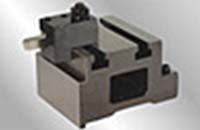
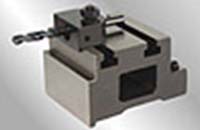
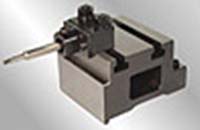
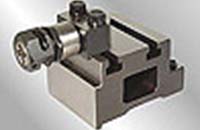
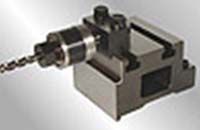
Samples of Matal and Non-Metal Machining
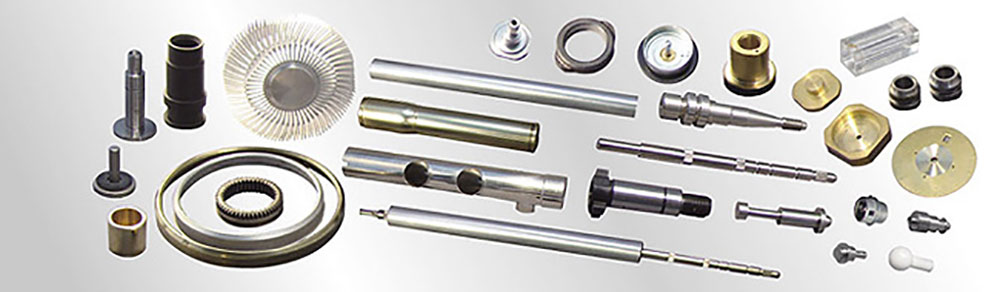
Features
- Guaranteed circular accuracy to 50 millionths of an inch
- Fanuc 0i mate-TF controller(standard), optional with other brand controller
- Powerful 3 HP motor (5HP-Option) with Yaskawa current vector inverter drive for improved torque response at low end
- Spindle mounted on high precision preloaded angular contact ball bearings
- Precision ballscrew on X and Z axes
- Protection guard on Z-axis ballscrew
- X, Z axes feeds drven by AC servo motor
- X, Z axes ballscrews directly coupled to AC servo motor, minimizing backlash
- Fast lever collect chucking
- Power collet closer
- Optional gang tooling
- Wide variety of accessories to increase versatility
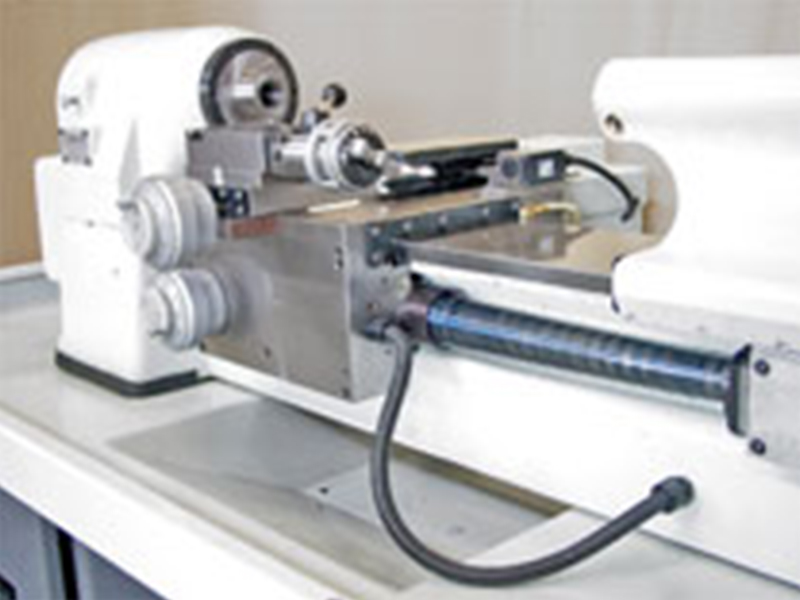
The saddle slideways are coated with Turcite-B for maximum wear resistance.
The cross slideways have hardened and ground tool steel inserts for smooth accurate movement.
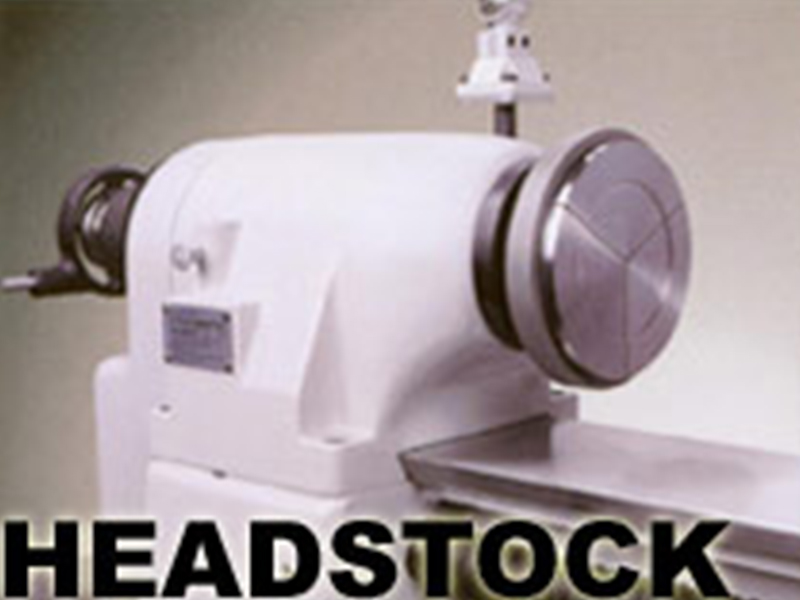
High-precision preloaded ball bearing spindle is mounted in the solid one-piece enclosed
headstock, providing maximum rigidity and sustained precision.
The collet seats directly in the hardened and precision ground
spindle, eliminating troublesome sleeves and adapters that introduce
costly inaccuracies.
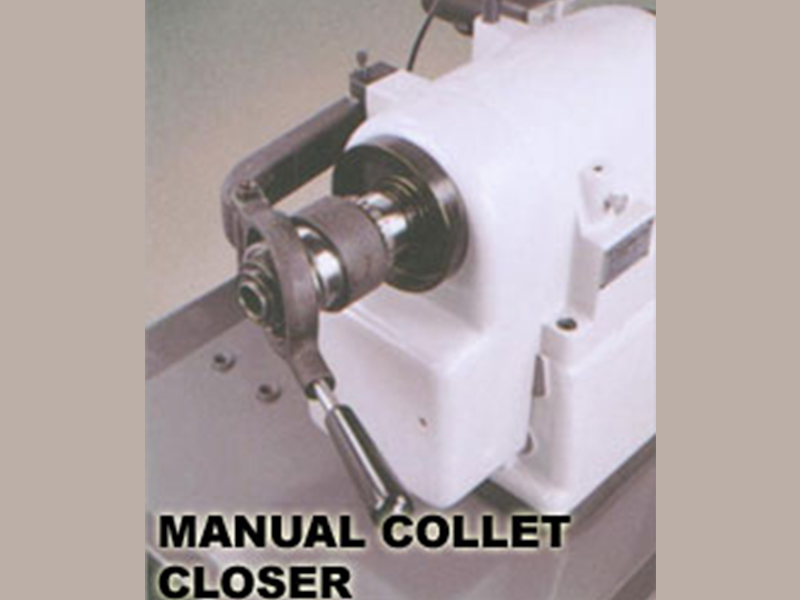
The fast lever collet closer provides faster chucking. The lever
control end of the closer assembly is balanced and rides on a
precision bearing. Collet tension is instantly adjustable throughout
the full range from light to heavy holding power without the use of
tools.
The spindle handwheel is built into the end of the
spindle.
Entire collet closer is conveniently removed by pulling
up the lock pin.
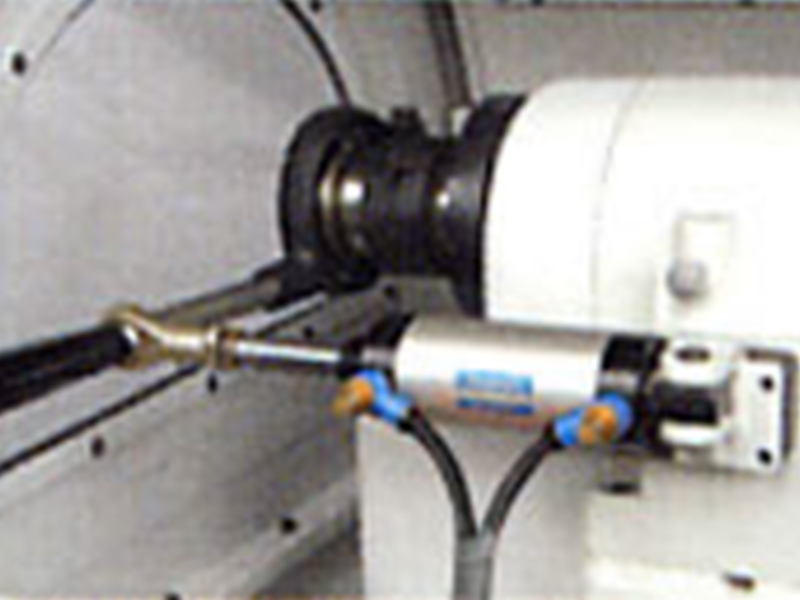
The lathe fit with a easy type power collet closer to replace manual lever operation, this air operated collet closer features automatic chucking.
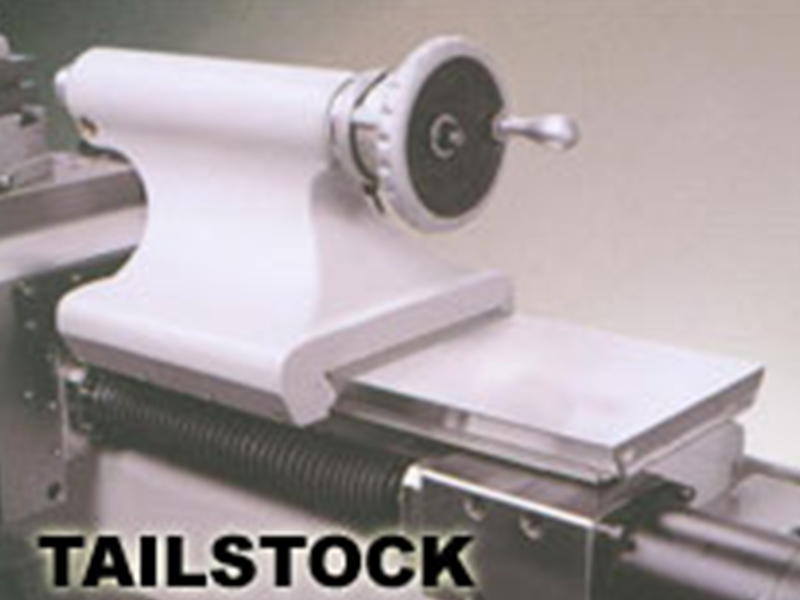
The solid full bearing tailstock supports any load to the preloaded ball bearing spindle headstock, The tailstock has 95mm(3-3/4") travel. The tailstock spindle is graduated in inch and metric for easy reading. Shank of MT#2 taper tools can be automatically discharged for easy operation.
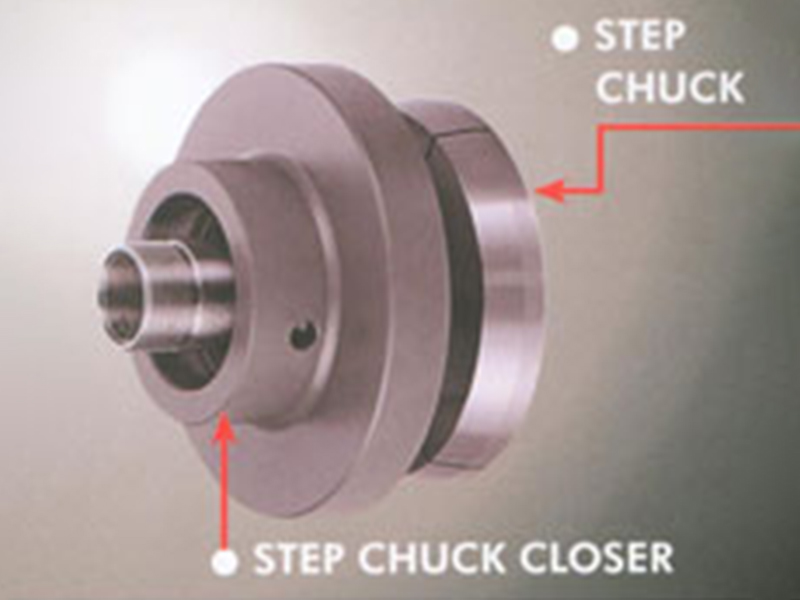
STEP CHUCKS are exceptionally useful for accurately holding work up to 6" in diameter. Castings, moldings, stampings and machined parts are held rigidly and accurately. Tubes can be held without crushing or distorting.
STEP CHUCKS AND CLOSERS are carried in stock in 2", 3", 4", 5" and 6" rated sizes. All step chucks are supplied with pin holes in place for precision machining.
CHUCK CLOSERS fit directly to the machine spindle. A taper corresponding to that on the periphery of the step chuck places the closing pressure over the stepped area of the chuck, resulting in greater gripping power and accuracy.